
-24-1.jpg)
Stainless Steel Reactor
Stainless Steel Reactor: used in dairy products, sugar, beverages, and other fields
Material
stainless steel (316, 304)
Capacity (L)
10-10000+
Mixing system
anchor, paddle, frame and others
Heating system
electric heating, oil heating and others
A stainless steel reactor is a stainless steel container equipment. The stainless steel reactor consists of a kettle body, a kettle lid, a stirrer, a jacket, a bracket, a transmission device, a shaft seal device, etc. Materials and openings can be made according to user needs and process requirements. Stainless steel reactors are mainly used for stirring, homogenizing, and mixing storage of dairy products, sugar, beverages, food, and various pharmaceuticals.
Request a quoteA stainless steel reactor is suitable for flammable, explosive, and other precious media and other high permeability materials. The reactivity of chemical media has now become an indispensable part of polymer material synthesis, food, and other processes. It is an ideal reaction equipment for necessary hydrogenation, oxidation, and other reactions.
During long-term use of stainless steel reactors, it is easy to accumulate a large amount of dirt, which affects the normal operation of the stainless steel reactor, increases energy consumption, and reduces product quality. Long-term use of stainless steel reactors can easily produce residual reactants, which gradually deposit in the stainless steel reactor. Not only does it affect the reactivity, but the components in the residue can also affect the reaction, thus adversely affecting the quality of the reaction. It can even cause serious safety problems and endanger the safety of personnel and equipment.
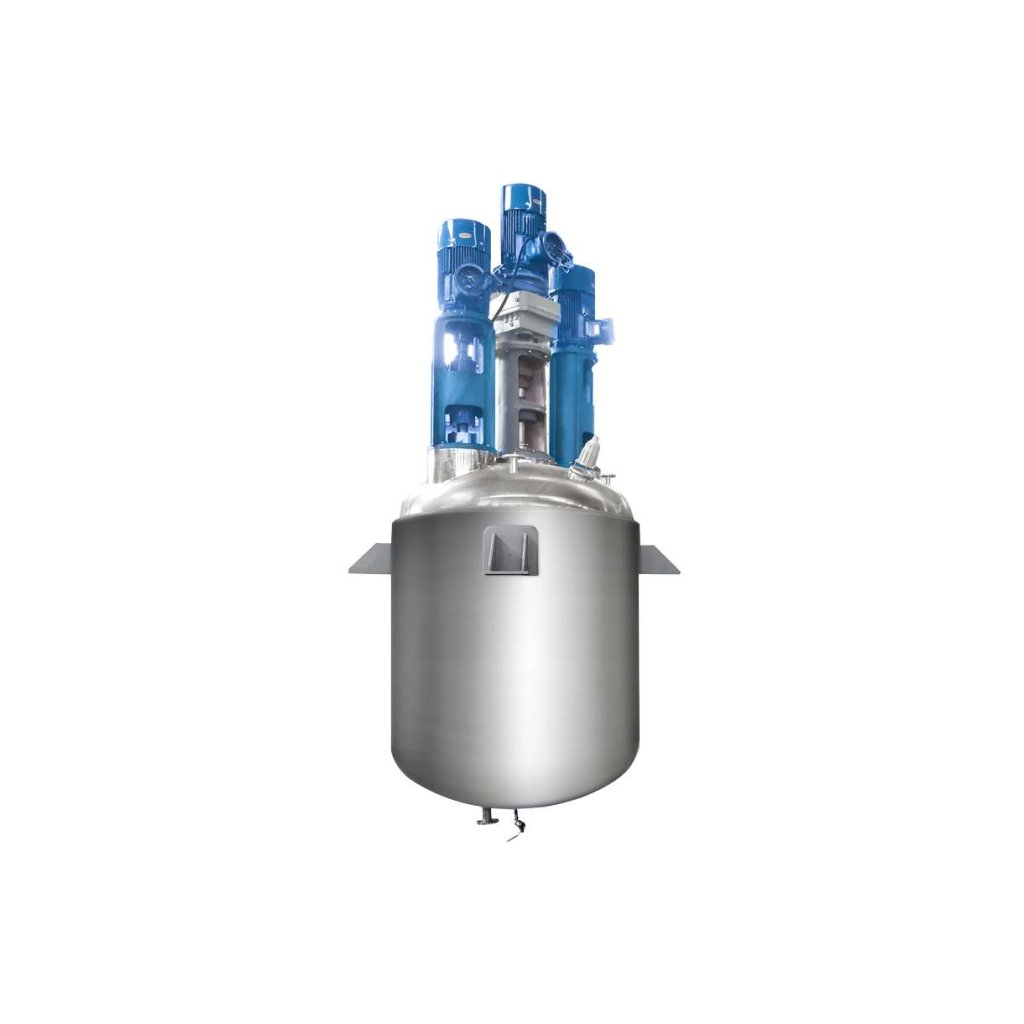
Precautions for stainless steel reactor
1. Low production efficiency
① Due to low heat transfer performance, the reaction time increases.
②. It should be noted that even if there is only a thin layer of dirt attached to the stainless steel reactor, the heat transfer performance will be greatly reduced.
2. Product quality declines
①. The dirt attached to the inner wall of the stainless steel reactor falls off, and foreign matter such as the residue of the kettle is mixed in. Moreover, the reaction time is longer due to the adhesion of dirt, resulting in the generation of heterogeneous reactants, resulting in product discoloration and inconsistent product quality.
②. Not only stainless steel reactors with a small number and many varieties, but also continuous reactors, once such problems occur, the losses will be huge.
3. Increased corrosion
Dirt will affect the service life of the stainless steel reactor itself. The “corrosion” referred to here is the localized battery effect caused by the concentration of liquid in the gaps between dirt and the inner surface of the kettle. This will form pitting corrosion, stress corrosion, etc. on the surface where dirt adheres, thereby reducing the service life of the stainless steel reactor.
4. Other impacts
①. If the thermometer inserted into the stainless steel reactor is stained, it will delay the temperature measurement, thus affecting the entire reaction control system.
② If dirt adheres to the mechanical shaft seal in the stainless steel reactor kettle, it may cause leakage of liquid in the kettle, or even the risk of explosion in the kettle.
③. Dirt adhering to the bearings and rotating parts in the stainless steel reactor will cause excessive vibration of the mixer, damage to the mechanical shaft seal, and affect the overall safety of the production device.