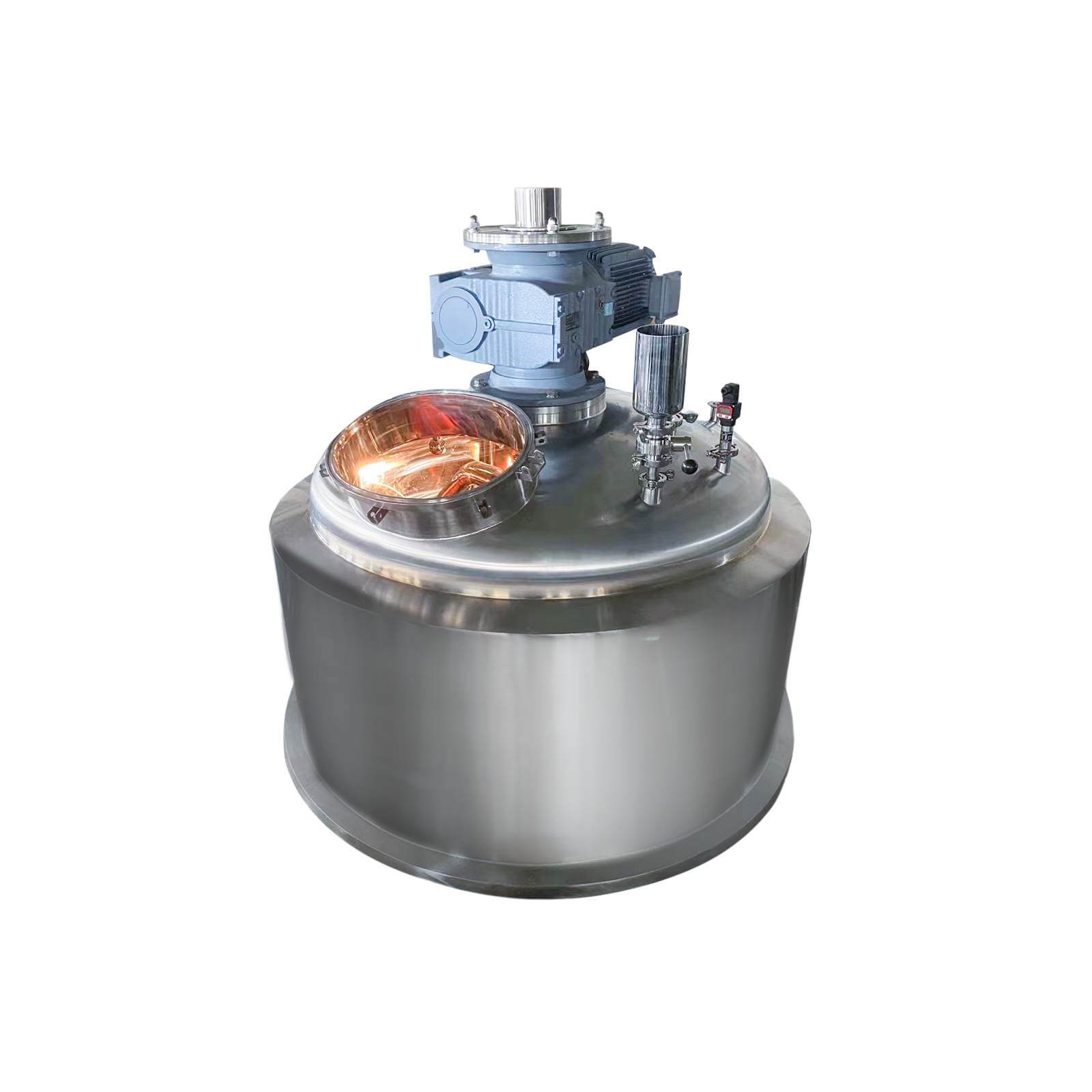
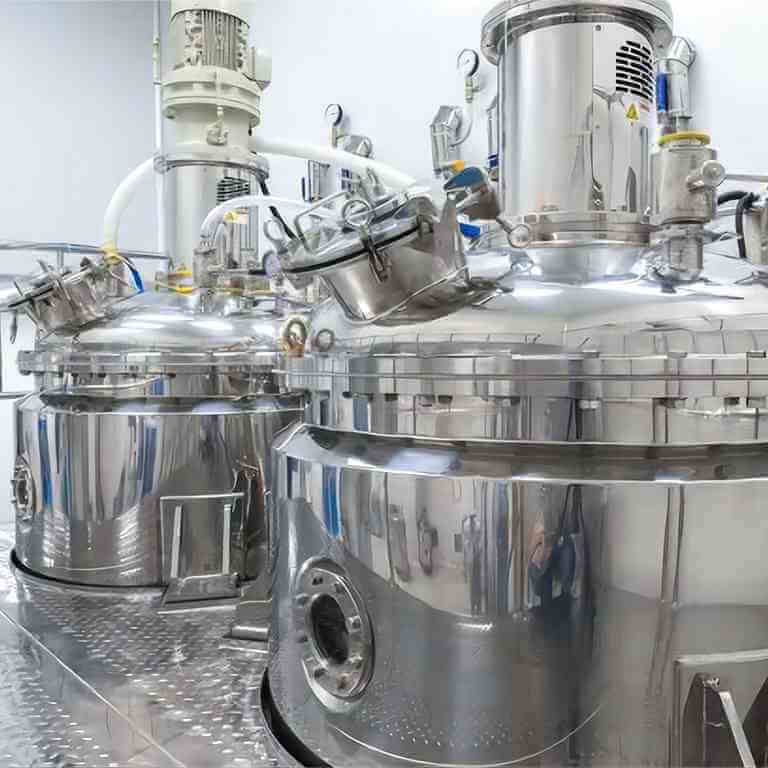
High Pressure Reactor
High-pressure reactor: used in chemical synthesis, catalytic reaction, and other fields
Material
glass, stainless steel (316, 304), carbon steel, others
Capacity (L)
10-10000+
Mixing system
anchor, paddle, frame and others
Heating system
electric heating, oil heating and others
The High-pressure reactor is mainly made of the kettle cover, the kettle body, the strong magnetic coupling stirrer, the high temperature, and high-pressure needle valve, the lower stirring part, the inner cooling coil, the temperature measuring part, the liquid lower pipe, etc.
Request a quoteThe high pressure reactor is an innovation of typical reaction equipment applied to magnetic transmission devices. It fundamentally solves the problem of shaft seal leakage that cannot be overcome by packing seals and mechanical seals in the past. It has no leakage and pollution. It is an ideal domestic chemical reaction under high temperatures and high pressure. The reaction device is especially suitable for chemical reactions of flammable, explosive, and toxic media, and shows its superiority. At the same time, we cannot ignore the safety problems caused by the high pressure reactor, among which its sealing is the most important thing we pay attention to.
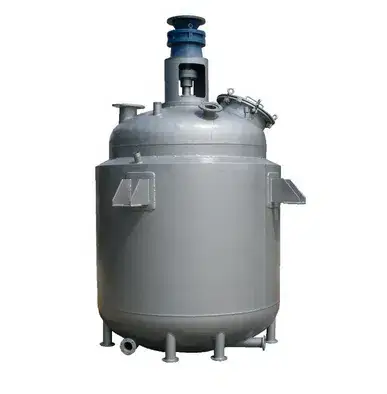
The sealing structure of a high pressure reactor
The high pressure reactor kettle adopts a quick-open lid structure, which can be opened in a short time; the lid of the kettle is equipped with a hand-rotating structure, which can rotate more than 120 degrees around the horizontal line, which is convenient for cleaning residues in the kettle. Ordinary double-head mechanical seals are often not ideal in actual use. The mechanical seal of this structure mainly has the following disadvantages when it is used on the high pressure reactor: The stirring shaft of the high pressure reactor generally swings greatly. The mechanical seal of this structure cannot solve this problem well, resulting in the seal being prone to failure.
The swing of the high pressure reactor shaft will cause the O-ring of the rotor ring to be squeezed and rotted; the drive pin will be bent or broken; the moving ring will lose buoyancy due to the deflection of the shaft, and the sealing surface of the moving ring will be tensioned prematurely. When the working pressure of the high pressure reactor is greater than 2.5mpa, the set screw of the spring seat is easy to slip, causing the seal to fail. For this reason, the mechanical seal of the structure should also be provided with a shaft sleeve, otherwise, the main shaft is easily slipped and scratched by the screw waste provided. In addition, if the shaft sleeve is not installed, the swing of the shaft will wear the O-ring of the shaft; the coolant should be fed from the inlet with medium pressure, so the mechanical seal should be equipped with a pressure cooling circulation system, which increases investment. A pressure oil cooling circulation system is generally used; due to the coolant pressure, the entire sealed cavity is required.
The seal chamber, shaft sleeve, and mechanical seal parts should be designed as assembled, which increases the cost; the load coefficient K of the mechanical seal of the structure cannot be adjusted too small. Therefore, the specific pressure of the end face is too high, and the seal friction pair wears seriously, resulting in a short life of the mechanical seal; the structure of the mechanical seal is complicated, and it is difficult to install and disassemble.
To improve the buoyancy of the mechanical seal of the high pressure reactor, special attention should be paid to the adjustment of the gap between the various parts of the seal. If the gap between the moving coil and the shaft sleeve is too large, the moving coil seal is easily crushed or broken. If the gap is too small, it is easy for the moving ring to be stuck. The gap between the moving coil and the spring seat, the upper static coil, and the shaft sleeve should be strictly controlled. The high pressure reactor equipment is huge, there are many connections, the factors affecting the installation quality increase, and the technical level of the installation workers is required.
The shaft (bush) end of the high pressure reactor installation moving ring should have edges and corners and be ground, and the static shaking of the shaft should not exceed 0.5mm. The radial swing of the shaft under the static ring should not exceed 0.5mm. The installation requirements of mechanical seals for high pressure reactors are by the drawings and design requirements. There should be a gap of 3-5mm between the dynamic ring seal ring and the dynamic ring seal chamber of the balanced mechanical seal. When installing the static ring, the end face should be aligned with the dial, and the perpendicularity between the end face and the axis should be 0.05mm. The spring compression allows an error of 2mm according to the drawings. After the installation is complete, loosen the nuts and start again. When the mechanical seal is installed, it should run dry for more than 24 hours. The mechanical seal is an anti-leakage device that realizes shaft sealing by a pair or several relative sliding end faces perpendicular to the shaft under the action of fluid pressure and the elasticity (or magnetic force) of the compensation mechanism combined with an auxiliary seal that holds the paste.
The mechanical seal structure commonly used in high pressure reactors consists of a static ring, a moving ring, an elastic element, a spring seat, a set screw, an auxiliary sealing ring for the moving ring, and an auxiliary sealing ring for the static ring. The anti-rotation is fixed on the cover to prevent the static ring from rotating. Rotating rings and stationary rings are also often referred to as compensating rings or non-compensating rings, depending on whether they have axial compensation capabilities.
It is particularly important to select a suitable sealing form for the high pressure reactor according to the conditions of use. At the beginning, the basis for sealing selection must be clarified. First, determine the working pressure in the high pressure reactor, then determine the nature of the working material, and the operating temperature of the equipment. Determining a suitable sealing form can not only ensure that the high pressure reactor meets the use conditions but also avoid unnecessary waste.