
-24-1.jpg)
Stainless Steel Reactor
Stainless Steel Reactor: used in dairy products, sugar, beverages, and other fields
Material
stainless steel (316, 304)
Capacity (L)
10-10000+
Mixing system
anchor, paddle, frame and others
Heating system
electric heating, oil heating and others
A stainless steel reactor is a stainless steel container equipment. The stainless steel reactor consists of a kettle body, a kettle lid, a stirrer, a jacket, a bracket, a transmission device, a shaft seal device, etc. Materials and openings can be made according to user needs and process requirements. Stainless steel reactors are mainly used for stirring, homogenizing, and mixing storage of dairy products, sugar, beverages, food, and various pharmaceuticals.
Request a quoteChemical production companies have multiple sets of chemical reactor kettles and distillation towers. The entire production system consists of multiple production units. Each production unit consists of one or more chemical reactors, condensers, and distillation towers. During the operation of the chemical reactor in the unit system, the atmospheric pressure chemical reactor and condenser used for liquid material transportation and exothermic reaction are used as the simplest operating units. Possible dangers and harmful factors were analyzed, corresponding measures were proposed, and safety instructions were formulated.
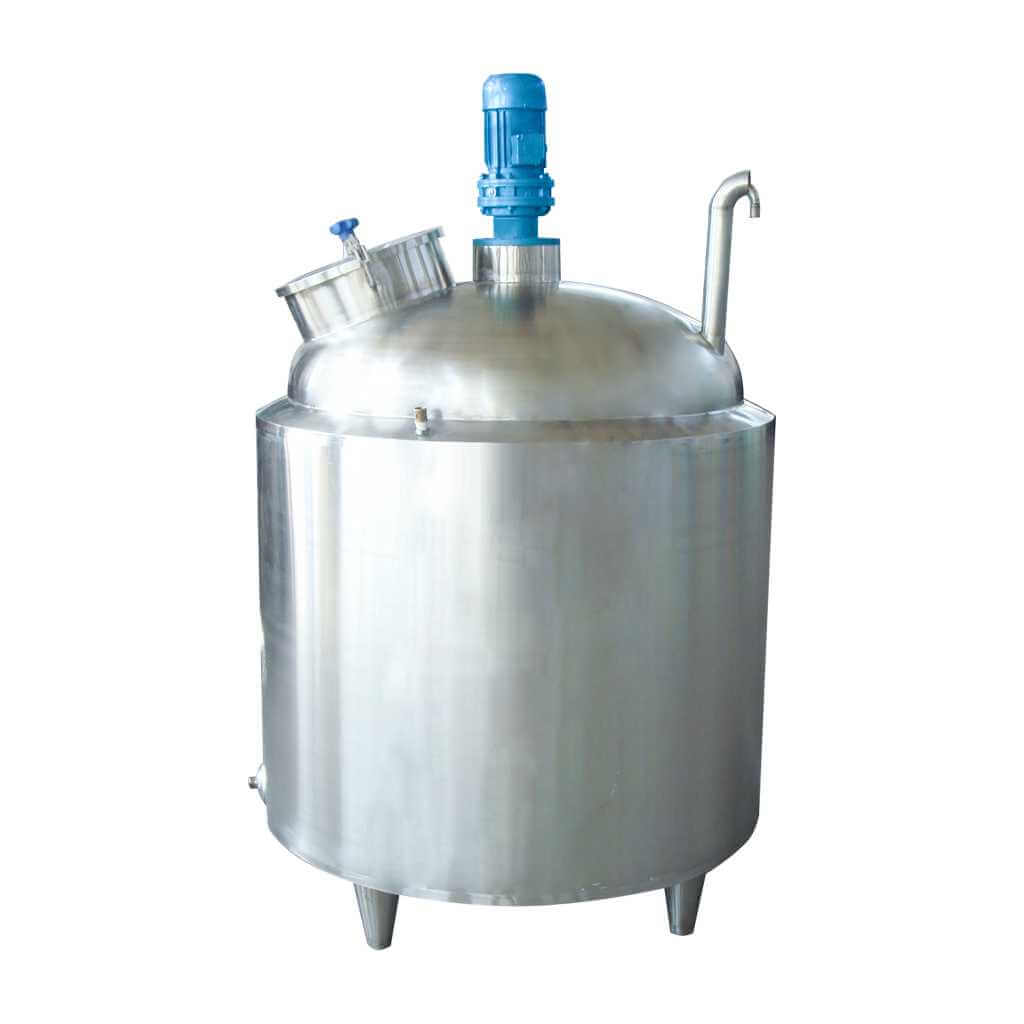
Main risk factors of chemical reactors
1.Feeding error
If the feeding speed of the chemical reactor is too fast, the feeding ratio is wrong or the feeding sequence is wrong, a rapid exothermic reaction may occur. If the cooling cannot be synchronized, heat accumulation will be formed, causing the material to be partially heated and decomposed, which will cause a rapid reaction of the material And produce a large amount of hazardous gas explosion accidents.
2.Pipeline leakage
When feeding materials, for the normal pressure reaction, if the vent pipe of the chemical reactor kettle is not opened, when the pump is used to transport the liquid material into the kettle at this time, a positive pressure is easily formed in the kettle, which may easily cause the joint of the material pipe to burst, and the leakage of the material may cause Personal injury burn accident. When unloading, if the material in the chemical reactor is not cooled to the specified temperature (generally required to be below 50°C), the material at a higher temperature is easy to deteriorate and may cause the material to splash and burn the operator.
3.Heating up too fast
The material in the chemical reactor kettle is heated too fast, the cooling rate is low, and the condensation effect is poor, which may cause the material to boil, form a vapor-liquid mixture, and generate pressure. , bursting discs, and other pressure relief systems implement pressure relief punching. If the punching material cannot achieve the effect of rapid pressure relief, it may cause an explosion accident of the chemical reactor body.
Safety precautions for chemical reactors
1.Heating control measures
For the material heating system with a reaction temperature below 100°C, the chemical reactor kettle can be heated by steam and hot water in sections. In the case of ensuring that the material will not deteriorate due to local overheating, first use steam to heat it to about 60°C at a medium speed. To improve production efficiency, use 100°C boiling water to circulate heat, slowly raise the temperature to the temperature specified by the process, and keep it warm for reaction. In this way, segmental heating can improve production efficiency and at the same time prevent local high-temperature thermal decomposition or violent vaporization of materials, and then form a vapor-liquid phase mixture to cause a blasting material explosion. It can also improve the yield of material equilibrium reactions and reduce consumption costs.
2.Chain cooling measures
For exothermic reactions, the chemical reactor needs to be heated in the initial stage of the material reaction, but the reaction process will release heat, so the excess heat must be transferred quickly and effectively. The cooling system of chemical reactors in normal use is mainly jacket cooling and coil cooling, and the cooling liquid used is mainly circulating water and freezing liquid. Refrigerant liquids cool quickly but are expensive. In the case of abnormal reactions during the production process, especially when the temperature and pressure rise sharply, the operator will quickly evacuate the operation site for their safety, cannot effectively cut off the heating source, and cannot effectively turn on the cooling of the chemical reactor kettle system. For this reason, a cooling chain system for emergency opening of the chemical reactor should be set up in a remote place other than the operating post. It is best to be close to the steam valve of the steam sub-cylinder in the workshop. When closing the steam valve and cutting off the stirring power supply, turn on the cooling chain system at the same time, and implement measures such as heat cut off, power off, stop stirring, and rapid cooling to control the accident in the initial stage. Prevent the further expansion of the accident.
To realize the heating, evaporation, cooling, and low-speed high-speed mixing reaction required by the process, the chemical reactor is an indispensable equipment. However, because the maintenance of the chemical reactor is not in place, it is often heard that safety and environmental pollution accidents are caused, so attention should be paid to it during use. At the same time, understanding the risk factors in production can avoid problems in this area, and when an accident occurs, the problem can be found in time and solved quickly.