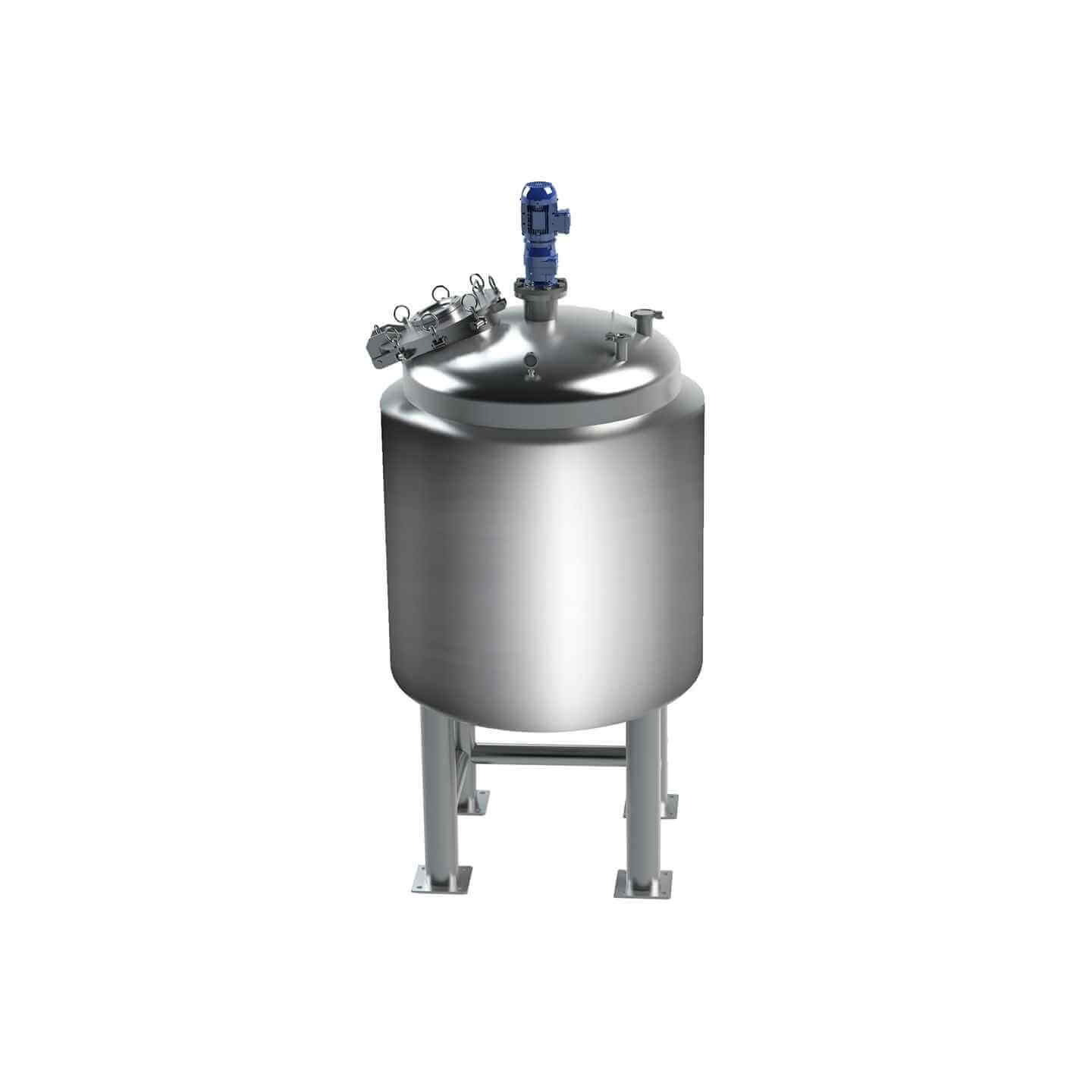
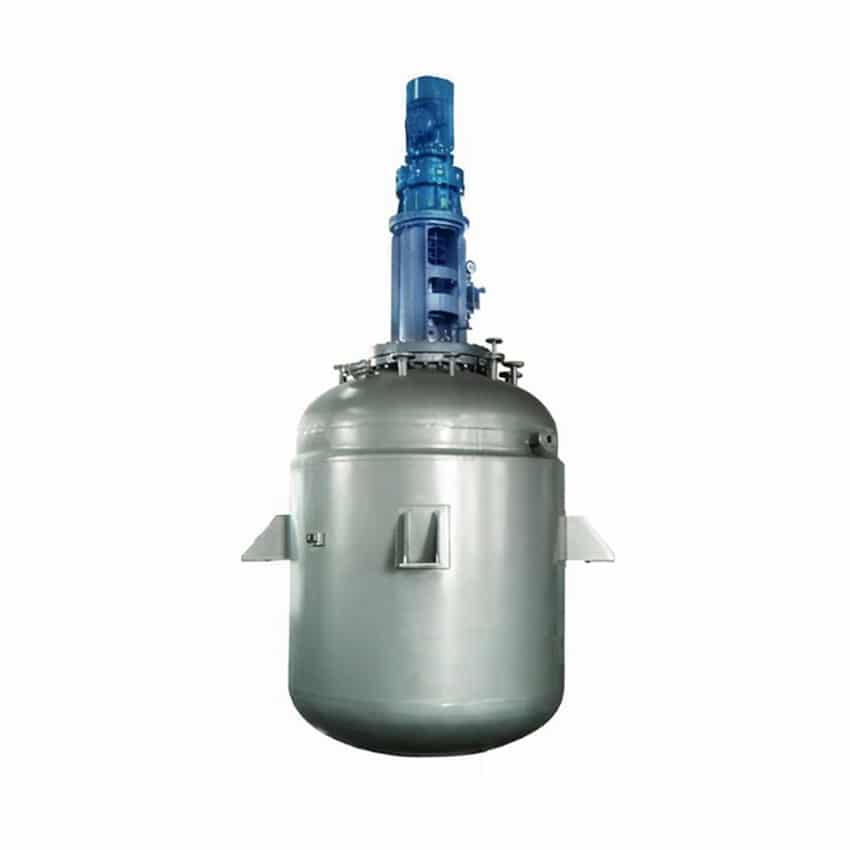
Jacketed Reactor
Jacketed reactor: used in the chemical industry, pharmaceutical industry and food industry, and other fields
Material
glass, stainless steel (316, 304), carbon steel, others
Capacity (L)
10-10000+
Mixing system
anchor, paddle, frame and others
Heating system
electric heating, oil heating and others
Jacketed reactors can be divided into steam heating reactors and heat transfer oil heating reactors according to different heating media, both of which are widely used in medicine, the chemical industry, plastics, rubber, building materials, food, and other industries. Corrosion, no environmental pollution, no need for automatic boiler heating, ease to use, and so on.
Request a quoteLarge capacity jacketed reactors are widely used in various fields such as organic chemistry, resins, coatings, and glues. In recent years, with the rapid growth of consumer markets such as the construction industry, decoration, and furniture industry, the artificial panel industry is also booming. Adhesives, which play an important role in the production of artificial panels, also play a decisive role in the cost of the product. As the production of artificial panels expands, the demand for adhesives increases and its quality and production costs have become important factors that directly affect the market competitiveness of artificial panel products and the profits of manufacturers. In order to reduce costs and reduce instability factors in adhesive production, it is becoming more and more common to use large capacity jacketed reactors in its production.
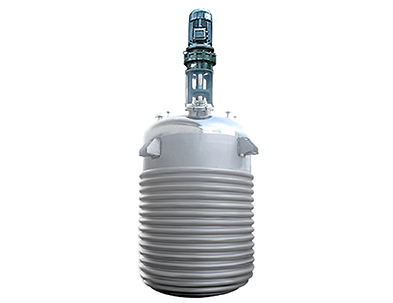
Technical features of large capacity jacketed reactor
Compared with traditional jacketed reactors, large capacity jacketed reactors have the following characteristics:
Large production capacity
The large capacity jacketed reactor uses a single layer kettle wall to replace the traditional jacketed kettle wall so that the reaction vessel does not bear or only bears small external pressure. Therefore, it gets rid of the limitations of traditional external pressure vessels such as excessive thickness of the kettle wall and poor heat transfer caused by the increase in volume. The volume of the large capacity jacketed reactor can reach 30m³ or even larger, which greatly improves the production capacity of a single reactor.
High heat transfer coefficient
The reaction medium is heated and cooled using the built in plate heat exchanger of the large capacity jacketed reactor, and the heat transfer coefficient is 40% higher than the traditional coil heat exchanger. Moreover, the plate heat exchanger has a compact structure, which is conducive to arranging sufficient heating and cooling areas in the large capacity jacketed reactor, making the synthesis reaction process of resin and glue more uniform and stable.
Easy to repair
Since the built-in plate heat exchanger of the large capacity jacketed reactor is detachable, it is easy to clean and repair, which helps reduce operating failures and improve production stability.
When the large capacity jacketed reactor is used in production practice, it can reduce the number of equipment, save factory investment, reduce operators, and reduce production costs. Therefore, large capacity jacketed reactors are increasingly used in the production of artificial board adhesives.
Commonly used materials for large-capacity jacketed reactors
In the design of large capacity jacketed reactors, reaction materials must also be considered. Commonly used reaction materials in reactions include:
1.Compatible or incompatible liquids. Mixing of liquids is easily achieved by stirring or mechanical mixing, and heat transfer to the reaction mixture is by convection.
2.Heterogeneous mixing of liquid and solid reactants of appropriate particle size. In this case, it is not possible to mix these materials completely with the help of a mixer. Once the mixing force of the large capacity jacketed reactor disappears, the materials in the reactor will settle to the bottom of the reactor to form a non-thermal conductive material layer and the following phenomena will occur:
1) The solid reactants are carbonized and the color of the mixture becomes darker.
2) The polymerization reaction is uneven and the polymer composition is uneven.
3) Carbonized materials, heat energy, and time are wasted.
4) Impact on the ecological environment due to waste of materials and energy. In order to avoid these problems, the reaction materials can be added multiple times in two steps:
① In the first step, add the liquid reaction materials to the large capacity jacketed reactor and heat the medium temperature to slightly higher than the reaction temperature or the melting point of the solid reactants.
②Slowly add the solid reactants while stirring in the large capacity jacketed reactor to allow it to react or dissolve continuously to avoid precipitation. However, this speed cannot be maintained accurately, and sometimes precipitation and coking may occur. And it takes a long time to complete the reaction.
Large capacity jacketed reactors require attention to many details during the production process. First of all, you should pay attention to the ratio of reactants to ensure that it is accurate. The second is temperature control. The large capacity jacketed reactor needs to maintain good temperature control during the reaction process to ensure the stability of the quality of the reaction product. In addition, the operation of the mechanical stirring device of the large capacity jacketed reactor also requires close attention to ensure good reaction results.