
-24-1.jpg)
Stainless Steel Reactor
Stainless Steel Reactor: used in dairy products, sugar, beverages, and other fields
Material
stainless steel (316, 304)
Capacity (L)
10-10000+
Mixing system
anchor, paddle, frame and others
Heating system
electric heating, oil heating and others
A stainless steel reactor is a stainless steel container equipment. The stainless steel reactor consists of a kettle body, a kettle lid, a stirrer, a jacket, a bracket, a transmission device, a shaft seal device, etc. Materials and openings can be made according to user needs and process requirements. Stainless steel reactors are mainly used for stirring, homogenizing, and mixing storage of dairy products, sugar, beverages, food, and various pharmaceuticals.
Request a quoteChemical reactors occupy a certain position in the field of fine chemicals and are widely used in chemical, biological, laboratory, resin, glue, and other industries. Its characteristics of high temperature and high-pressure resistance are deeply loved by people. Therefore, its safety issues are also highly valued by people. When the chemical reactor reaches a certain age, it needs to be repaired or replaced. This will not only ensure the normal operation of the chemical reactor but also prevent safety accidents from occurring.
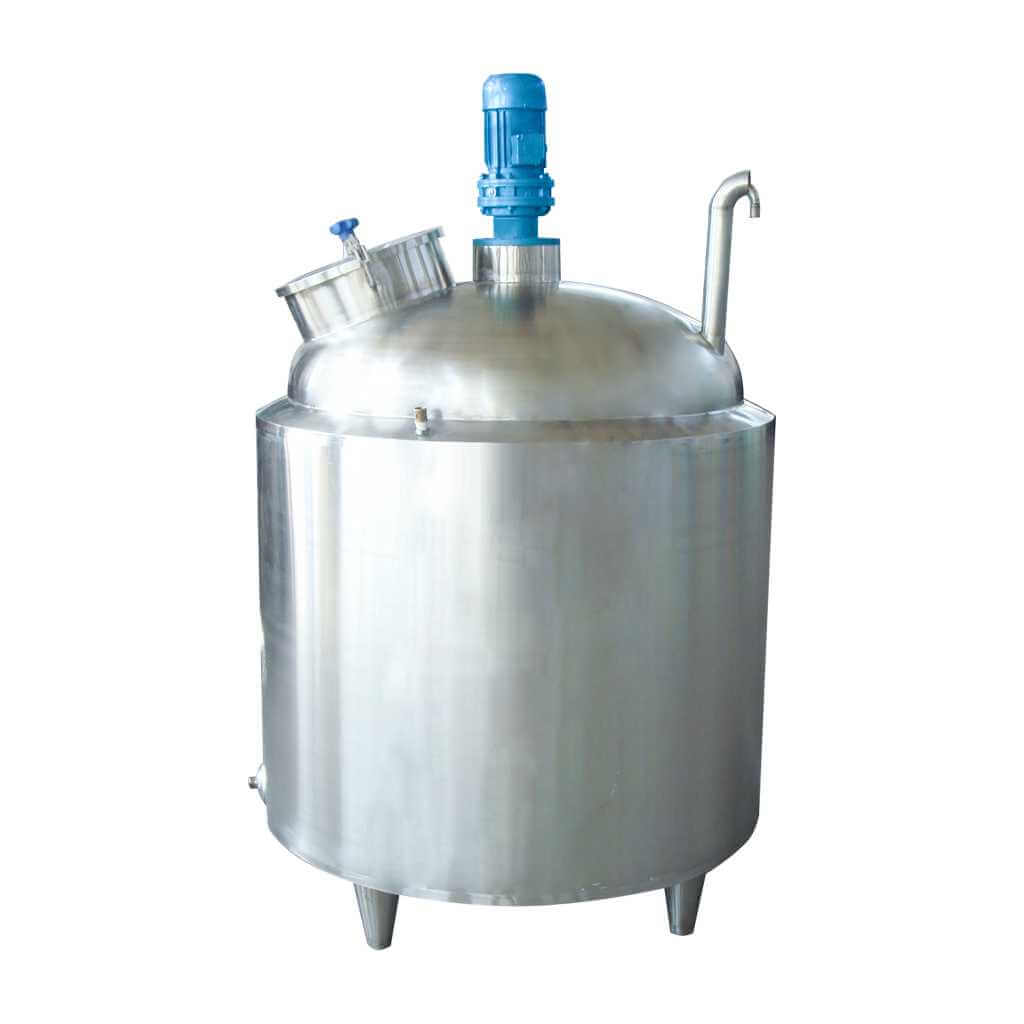
Replacement conditions for chemical reactors
1. When conducting a hydraulic test, the chemical reactor has obvious deformation or the residual deformation exceeds the specified value.
2. When the damaged area of the chemical reactor exceeds 15% or the damaged part cannot be repaired.
3. The uniform corrosion of the kettle wall thickness exceeds the minimum value specified in the design.
4. When the defects exceed the standard and cannot be repaired (such as serious structural defects endangering safe operation; unqualified welds; serious lack of penetration, cracks, etc.).
5. The local corrosion of the kettle wall thickness exceeds the minimum value specified in the design, and the corrosion area is greater than 20% of the total area.
6. Due to alkali embrittlement or severe intergranular corrosion, cracks in the chemical reactor kettle body or welds cannot be repaired.
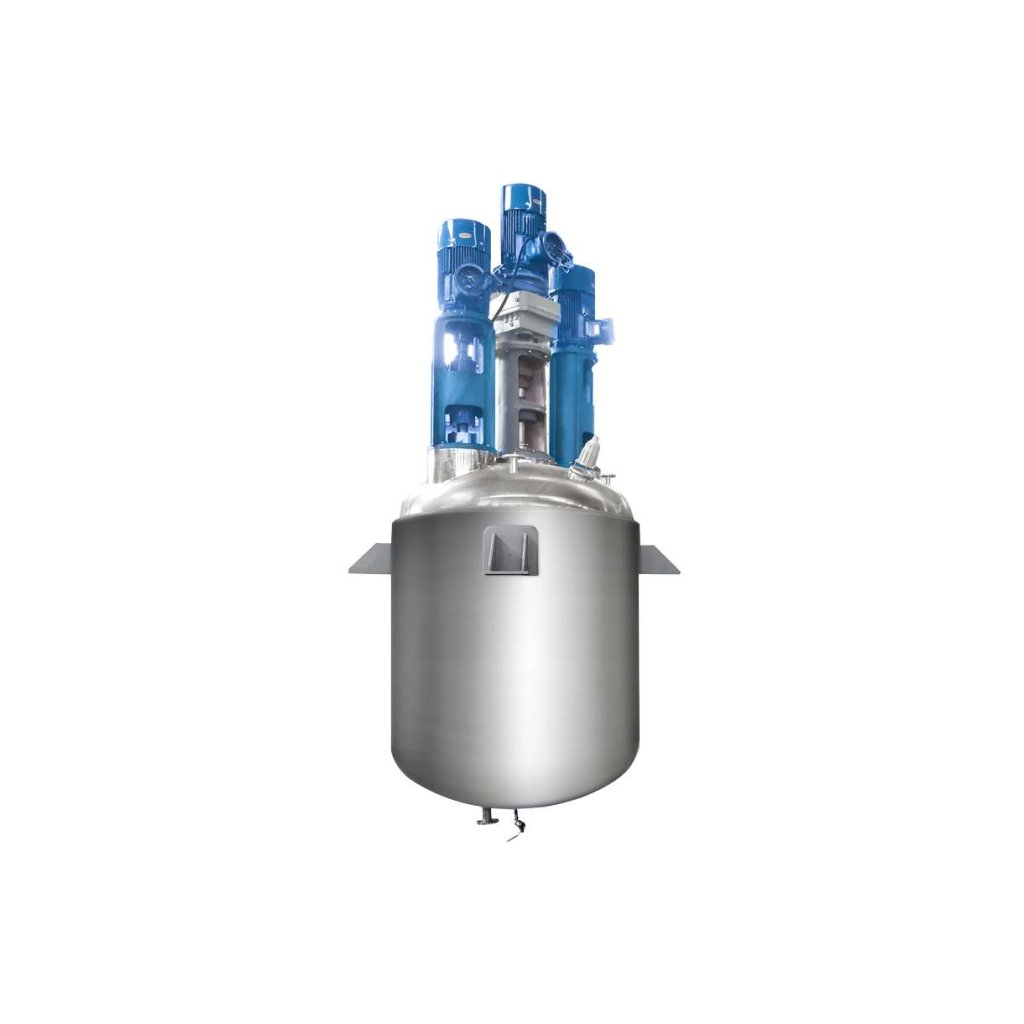
Kettle body repair of chemical reactor
1. Local corrosion of the kettle body: Use the arc surfacing method to repair. If the corrosion area of the chemical reactor is large, use the supplementary method to repair it.
2. Penetrating wide cracks: Wide cracks should be repaired by excavation and repair. The length of excavation and repair should be 50/100 mm longer than the length of the crack, and the width should not be less than 250mm. The welded patch plate should be flush with the surface of the chemical reactor kettle body, and the radius of curvature should be the same as the kettle body.
3. Penetrating narrow cracks: Before welding repair, drill anti-crack holes at both ends of the crack in the chemical reactor. The hole diameter is slightly larger than the width of the crack, and a groove is processed. When the wall thickness is less than 12mm, V-shaped grooves are used; when the wall thickness is greater than 12mm, X-shaped grooves are used. During welding repair, cracks with a length less than 100mm can be welded in one go; when the crack is longer, it is advisable to weld from both ends of the crack to the middle, do not draw an arc, and use multi-layer welding. Except for the parts where stress is concentrated, welding repairs are allowed for cracks and penetrating narrow cracks in various parts of the chemical reactor kettle body.
4. Unpenetrated cracks: If the depth of the crack in the chemical reactor is less than 10% of the wall thickness and not greater than 1mm, the crack can be smoothed with a grinding wheel and smoothly transitioned to the metal surface. If the crack depth of the chemical reactor does not exceed 40% of the wall thickness, a groove can be shoveled within the crack depth range for welding repair. However, small holes should be drilled at both ends of the crack to prevent the crack from extending. For long cracks, use the segmental de-welding method (segment-by-section welding from both ends of the crack to the middle) to reduce welding stress and deformation. If the crack depth of the chemical reactor exceeds 40% of the wall thickness, it should be treated as a penetrating narrow crack.
5. Stainless steel lining bulging: When the lining of the chemical reactor is deformed in a large area and the ratio of the lining bulging height to the average diameter of the deformed area is less than 0.15, it is advisable to use water filling and pressure boosting to restore the deformed liner. For the chemical reactor kettle body or lining with a small deformation area, mechanical pressing can be used to repair it, but care should be taken to prevent embrittlement during the correction process.
6. For common defects such as blisters, cracks, pitting corrosion, or local corrosion in chemical reactors, arc cold welding is usually used to repair them. During welding repair, a crack arresting through the hole should be drilled 3-5mm outside the crack endpoint.
Chemical reactors replace cumbersome intermittent manual operations with production automation and continuity, which can not only ensure stable production, improve product quality, increase profits, and reduce physical labor, but also eliminate environmental pollution. The chemical reactor is a kind of chemical reaction equipment that operates intermittently. The kettle body in contact with the reaction medium can be made of various types of stainless steel and non-ferrous metals such as titanium, nickel, and zirconium. During the reaction process, it has good corrosion resistance. Therefore, understanding its repair operations can quickly solve repair problems and avoid long repair times and production shutdown losses.