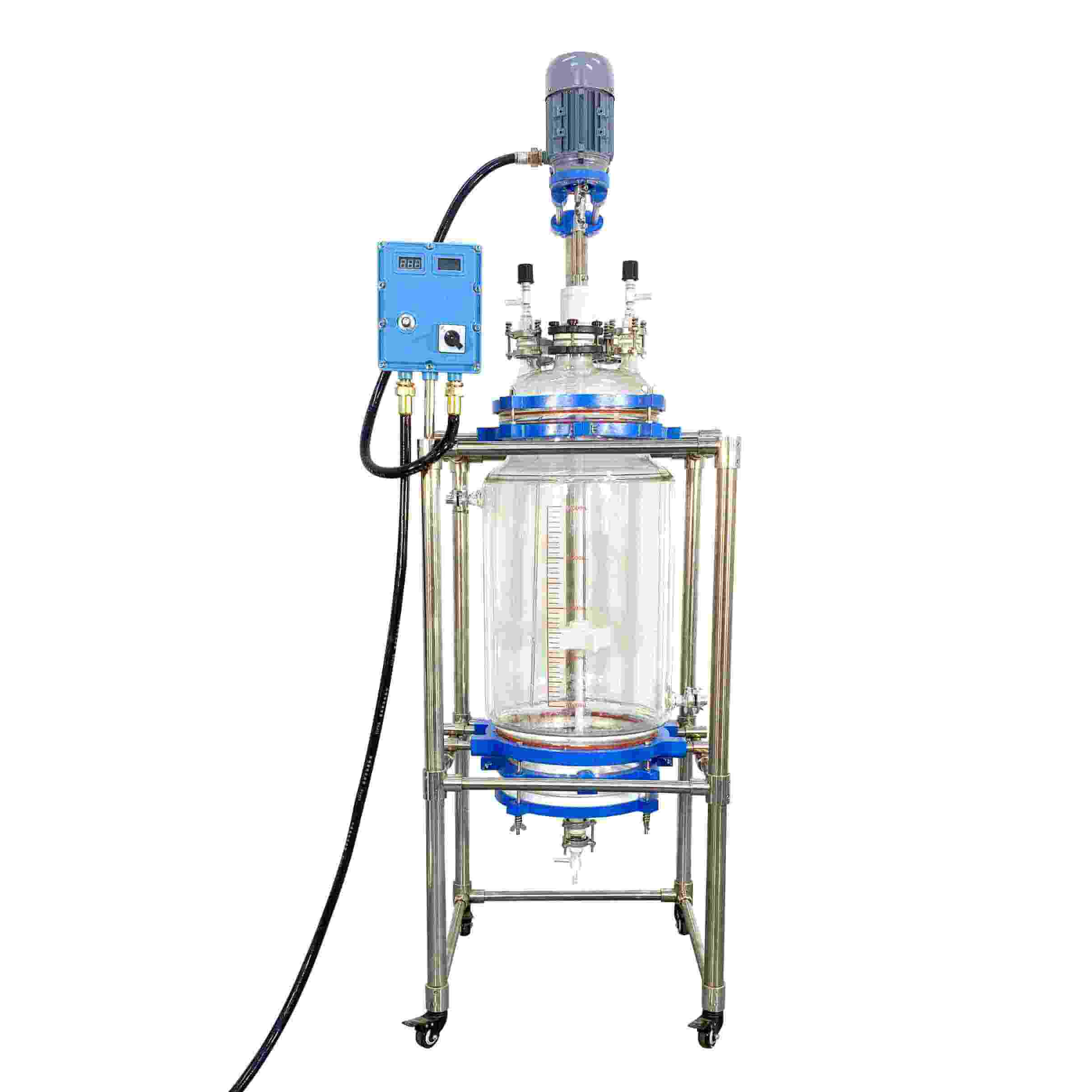
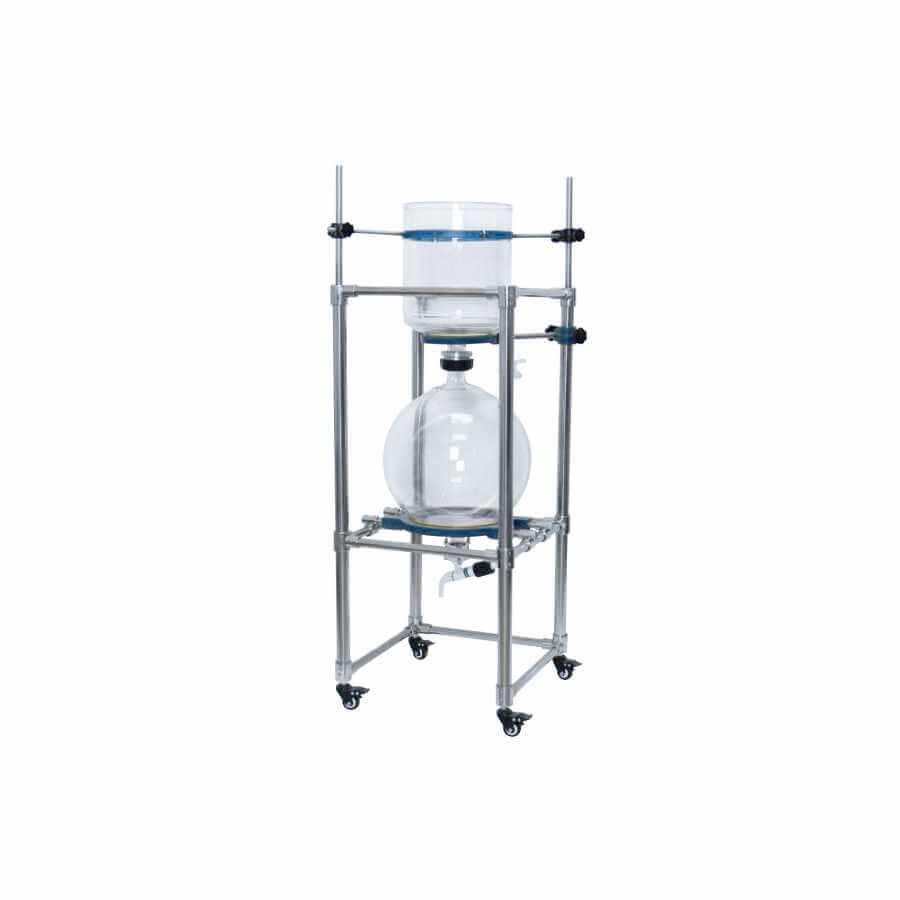
Glass Reactor
Glass reactors: used in chemical reactions, drug research and development, fine chemicals, food manufacturing, and other fields.
Material
glass
Capacity (L)
10-10000+
Mixing system
anchor, paddle, frame and others
Heating system
electric heating, oil heating and others
RUNGYU glass reactors are commonly used biochemical instruments and are widely used in modern fine chemicals, biopharmaceuticals, scientific research and experiments, and other industries. They can be used for concentration, distillation, reflux, separation, and purification reactions under the conditions of constant speed, constant force, and constant temperature. It is an ideal equipment for teaching, experiment, pilot test, and production.
Request a quoteThe glass reactor is a chemical reactor that controls the temperature of the reactants. Using a constant-temperature oil bath or a low-temperature circulation pump, the reactants are heated and cooled through the interlayer of the glass reactor, so that the temperature of the reactants in the glass reactor can be controlled at a very high level. It can significantly improve the efficiency and quality of experiments or production.
The materials react in the glass reactor, and the evaporation and reflux of the reaction liquid can be controlled. After the reaction is completed, the material can be discharged from the outlet at the bottom of the kettle, making the operation extremely convenient. Glass reactor is ideal equipment for modern chemical samples, media sample experiments, biopharmaceuticals, and new material synthesis.

Structural composition of glass reactor
1.Motor: The glass reactor uses a low-speed power-increasing motor and reducer to ensure that the equipment can stir for a long time. In addition, explosion-proof motors or brushless DC motors can be selected according to user needs.
2.Constant pressure dropping funnel: The glass reactor is equipped with a high vacuum polytetrafluoroethylene hand valve, which can ensure constant internal pressure and has the function of preventing back suction.
3.Universal joint: The universal joint has the function of changing the power transmission angle and connecting the motor and the stirring rod to make the mixing function of the equipment more stable.
4.Stirring slurry: The glass reactor is made of polytetrafluoroethylene, which is resistant to high temperature, corrosion, acid and alkali corrosion.
5.Stirring seal: PTFE component plus mechanical component double seal, ceramic bearing.
6.Vacuum gauge: The glass reactor kettle monitors the pressure inside the kettle in real-time.
7.Kettle cover: adopts a seven-hole design, which includes the stirrer port, temperature sensor port, condenser connection ball mill port, constant pressure funnel port, solid feeding port, drain valve, and liquid rubber material port.
8.Vacuum interlayer: plays a good thermal insulation role and prevents temperature loss.
9.Circulating fluid interlayer: The glass reactor heats or cools the experimental materials in the kettle by connecting low-temperature coolant circulating pumps, high and low-temperature integrated machines, and other equipment that can provide low-temperature or high-temperature circulating fluid.
10.Circulating fluid interlayer: The glass reactor heats or cools the experimental materials in the kettle by connecting low-temperature coolant circulating pumps, high and low-temperature integrated machines, and other equipment that can provide low-temperature or high-temperature circulating fluid.
11.Aluminum clamp and PTFE gasket: play the role of fixing the discharge valve and have good sealing performance.
12.No dead angle discharge valve: makes the discharge work clean and thorough, and the detachable design is conducive to the discharge of solids, particles, and high-viscosity experimental materials.
13.Exhaust valve: This protection can prevent accidental damage to the reactor during rotation and improve the safety of the glass reactor.
14.Vacuum suction port of the condenser: reduce the pressure of the condenser by connecting a vacuum pump to speed up the condensation efficiency of the condenser.
15.Cooling water supply: By connecting refrigeration cycle equipment such as a low-temperature coolant circulation pump, it provides low temperature to the condenser and speeds up the condensation efficiency of the condenser.
16.Coil condenser: The double-layer coil design increases the contact area between the condenser and gaseous substances and improves the condensation efficiency.
17.Silicone fixing ring: plays the role of fixing the condenser.
18.Liquid separator: used to separate liquid from liquid.
19.Drainage valve: controls the discharge of materials in the disperser.
20.Dual display panel for temperature and rotational speed: On the control panel of the whole machine, the temperature and rotational speed are displayed on the screen in digital form, making the operation simple and fast.
21.Vacuum sandwich air extraction port: used to evacuate the vacuum sandwich.
22.Kettle body support pipe fittings: used to fix and support the glass reactor body.
23.Stainless steel support frame: Full SUS304 stainless steel frame, with better corrosion resistance and heat resistance.
24.Casters with brakes: easy to move and more flexible to use.
Glass reactor is an ideal reaction equipment for modern chemicals, new materials, organic synthesis, biopharmaceuticals, precious metal purification, and other occasions.