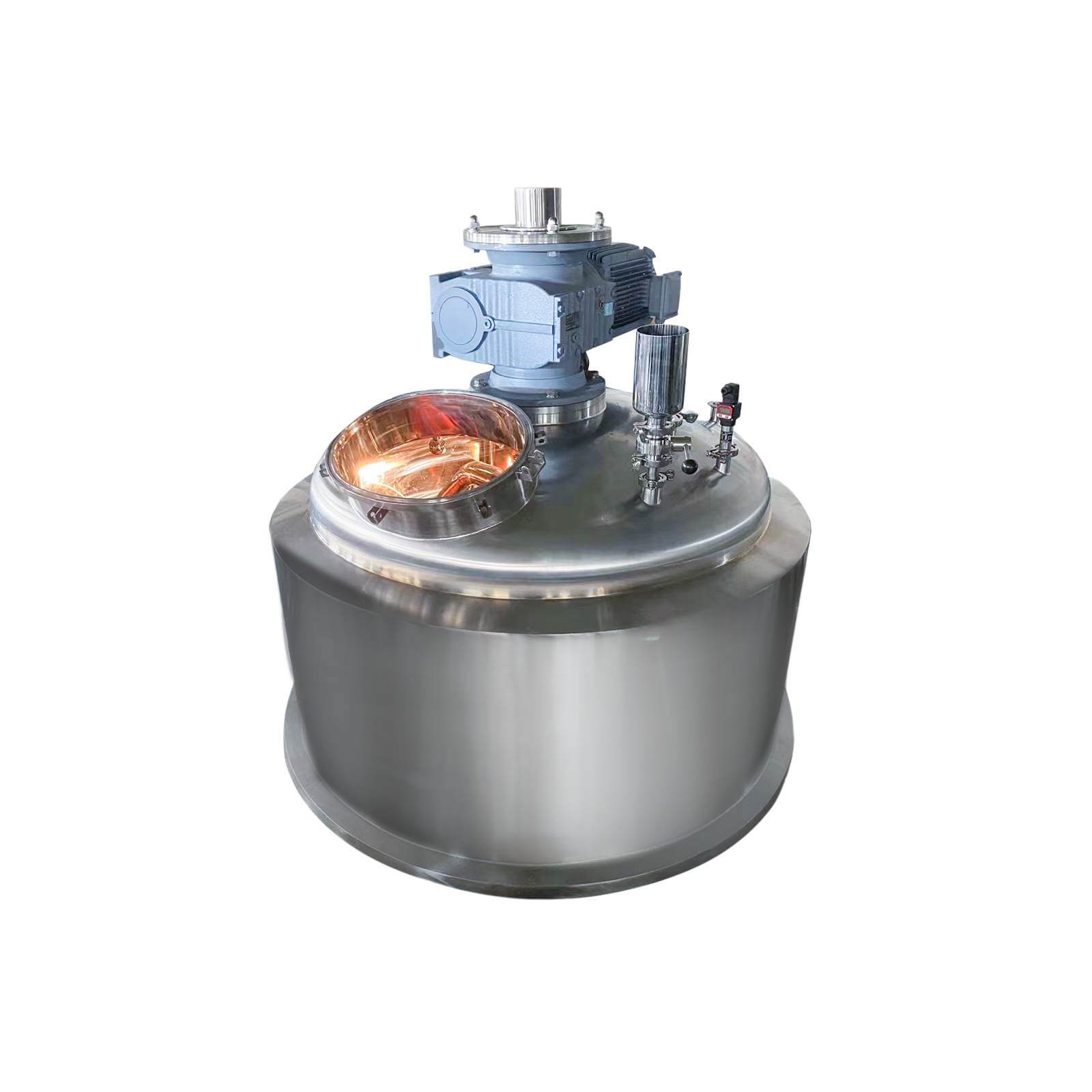
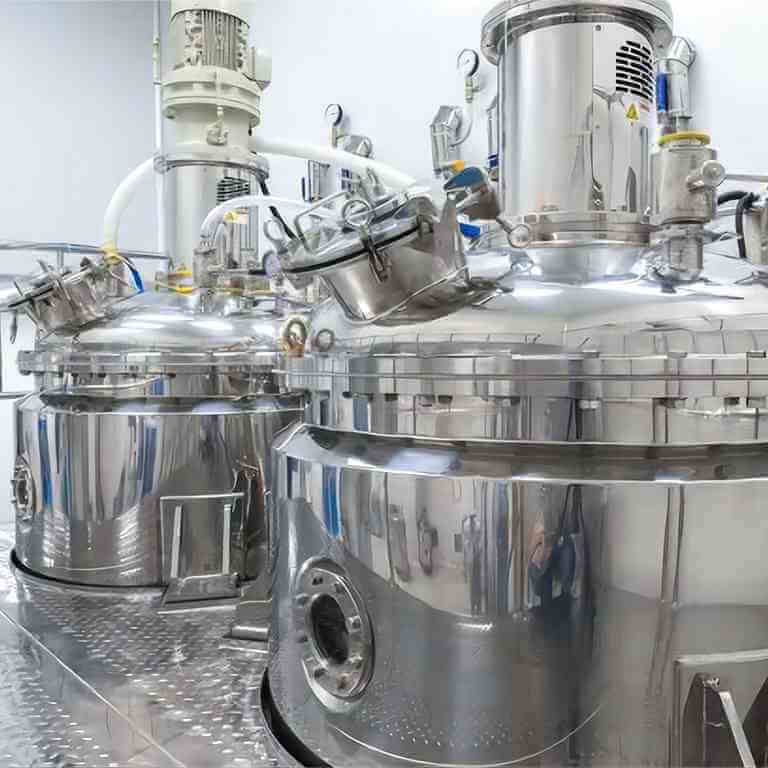
High Pressure Reactor
High-pressure reactor: used in chemical synthesis, catalytic reaction, and other fields
Material
glass, stainless steel (316, 304), carbon steel, others
Capacity (L)
10-10000+
Mixing system
anchor, paddle, frame and others
Heating system
electric heating, oil heating and others
The High-pressure reactor is mainly made of the kettle cover, the kettle body, the strong magnetic coupling stirrer, the high temperature, and high-pressure needle valve, the lower stirring part, the inner cooling coil, the temperature measuring part, the liquid lower pipe, etc.
Request a quoteAs commonly used equipment in chemical plants, high pressure reactors should be placed in high-pressure operating rooms that meet explosion-proof requirements. If multiple high pressure reactors need to be equipped in the factory, they need to be placed separately, and there should be reliable grounding at the same time. Every two devices should be separated by a feasible firewall to ensure that the devices will not affect each other. Each operating room should have an exit directly to the outside or a passage to ensure that the staff can leave safely in the event of an accident.
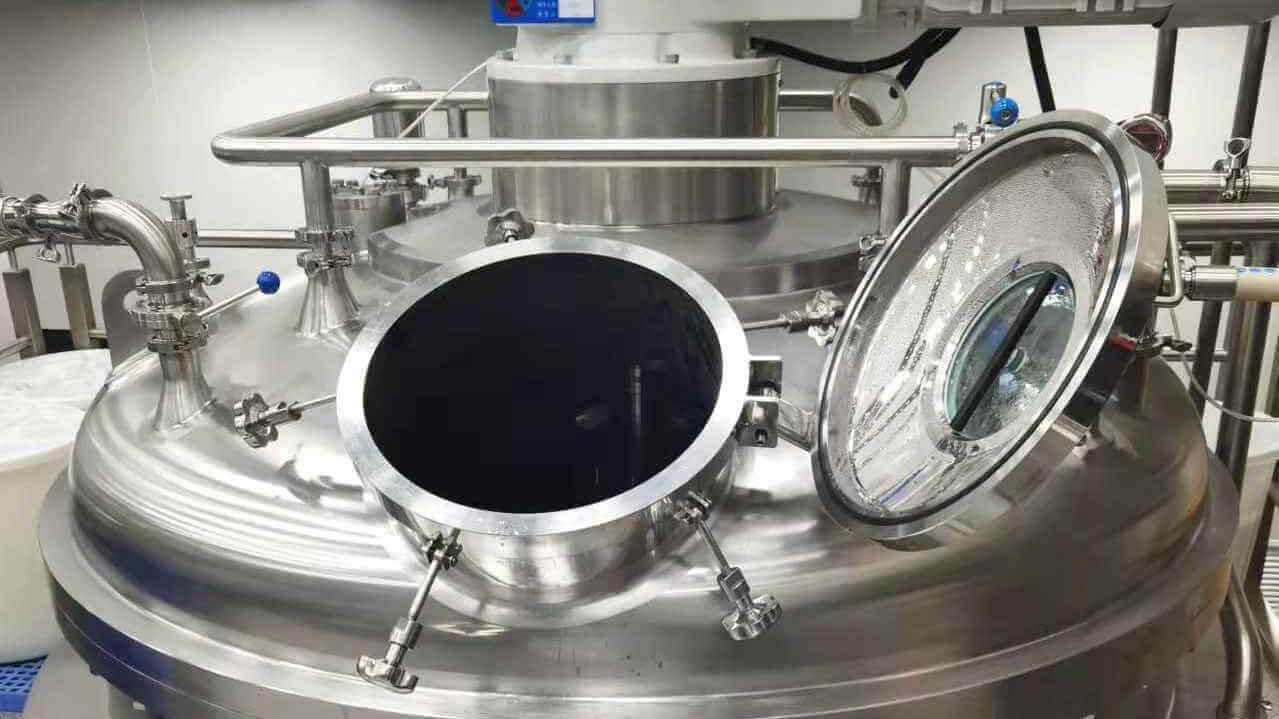
Installation of a high pressure reactor
When installing the cover of the high pressure reactor, first place the sealing ring, then install the cover to a fixed position and carefully place it on the kettle body. Between the pure copper sealing ring the kettle body and the kettle cover, the conical surface is used for sealing. By tightening the main bolts, they are pressed against each other to achieve the purpose of sealing. The sealing surface should be specially protected, otherwise, it will be easily damaged, resulting in incomplete sealing and incalculable losses. When tightening the main bolts, do not exceed the specified tightening torque to prevent the sealing surface from being crushed or accelerated wear. After the sealing surface is damaged, it needs to be reprocessed and repaired to restore good sealing performance. When tightening the bolts, they must be tightened diagonally and symmetrically several times, and the force must be uniform. The lid of the kettle is not allowed to tilt to one side, otherwise, a good sealing effect will not be achieved. All threaded connections need to be coated with oil or oil mixed with graphite during assembly.
When heating and pressurizing the tightness test, the test medium can be air or nitrogen, but it is better to use inert gas. Inert gas will be safer when conducting experiments. At the same time, it is strictly forbidden to use oxygen or other flammable and explosive gases. When raising the temperature and increasing the pressure, it must be done slowly. The heating rate should not exceed 80 degrees per hour. During the pressure test, connect the inlet valve of the high pressure reactor to the compressor (or high-pressure pump) with a connecting pipe. The pressure increase must be carried out in stages, with 20% of the working pressure as the interval, and it needs to stay for 5 minutes for each level, and it needs to stay for 30 minutes when it rises to the test pressure, and check the sealing condition. The test pressure is 100-105% of the working pressure. When a leak is found, the pressure should be reduced first, and then the nuts and joints should be properly tightened. It is strictly forbidden to tighten the nuts and joints under high pressure.
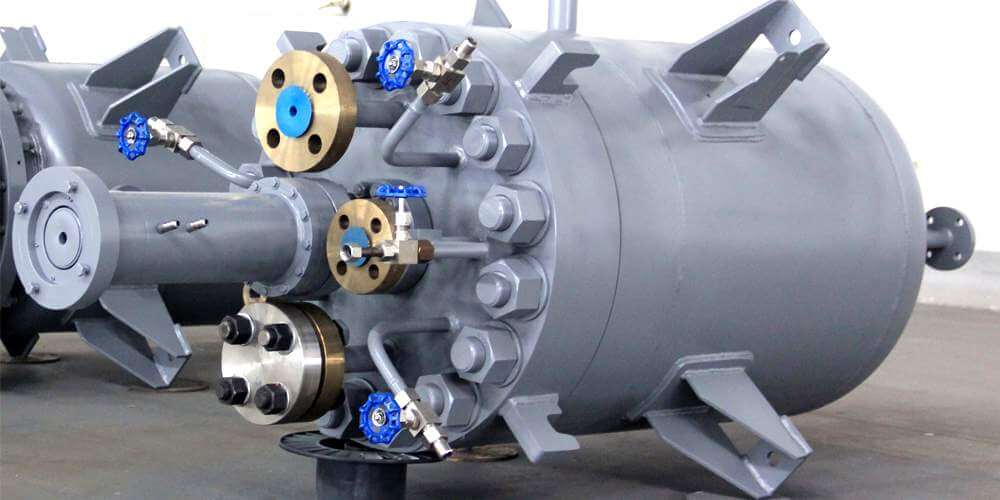
Use of high pressure reactor
Rapid cooling and rapid heating of the high pressure reactor are strictly prohibited to prevent the kettle body from bursting due to stress due to excessive temperature difference. After operation, water cooling (exothermic reaction) or air cooling can be used. The needle valve uses a wire seal. You only need to gently turn the needle and press the sealing surface to achieve a good sealing effect. Excessive force is prohibited to avoid damage to the sealing surface and cause unnecessary losses. After the reaction is completed, cool it first, then release the high-pressure gas in the high pressure reactor to reduce the pressure to normal pressure, and then loosen and remove the bolts symmetrically and evenly. When removing the cover, special attention should be paid to protecting the sealing surface of the high pressure reactor. After each operation, the residue on the kettle body and lid should be removed. All sealing surfaces on the high pressure reactor should be cleaned frequently and kept dry. Do not use hard objects or soft objects with rough surfaces for cleaning.
Understanding the correct installation steps of the high pressure reactor can avoid problems in the later stage and prevent immeasurable losses due to installation errors. At the same time, correct use can extend the service life of the high pressure reactor and bring more benefits. High pressure reactors work in a high-pressure environment. Once a problem occurs, the situation is uncontrollable, so it must be operated under the condition of ensuring personal safety.