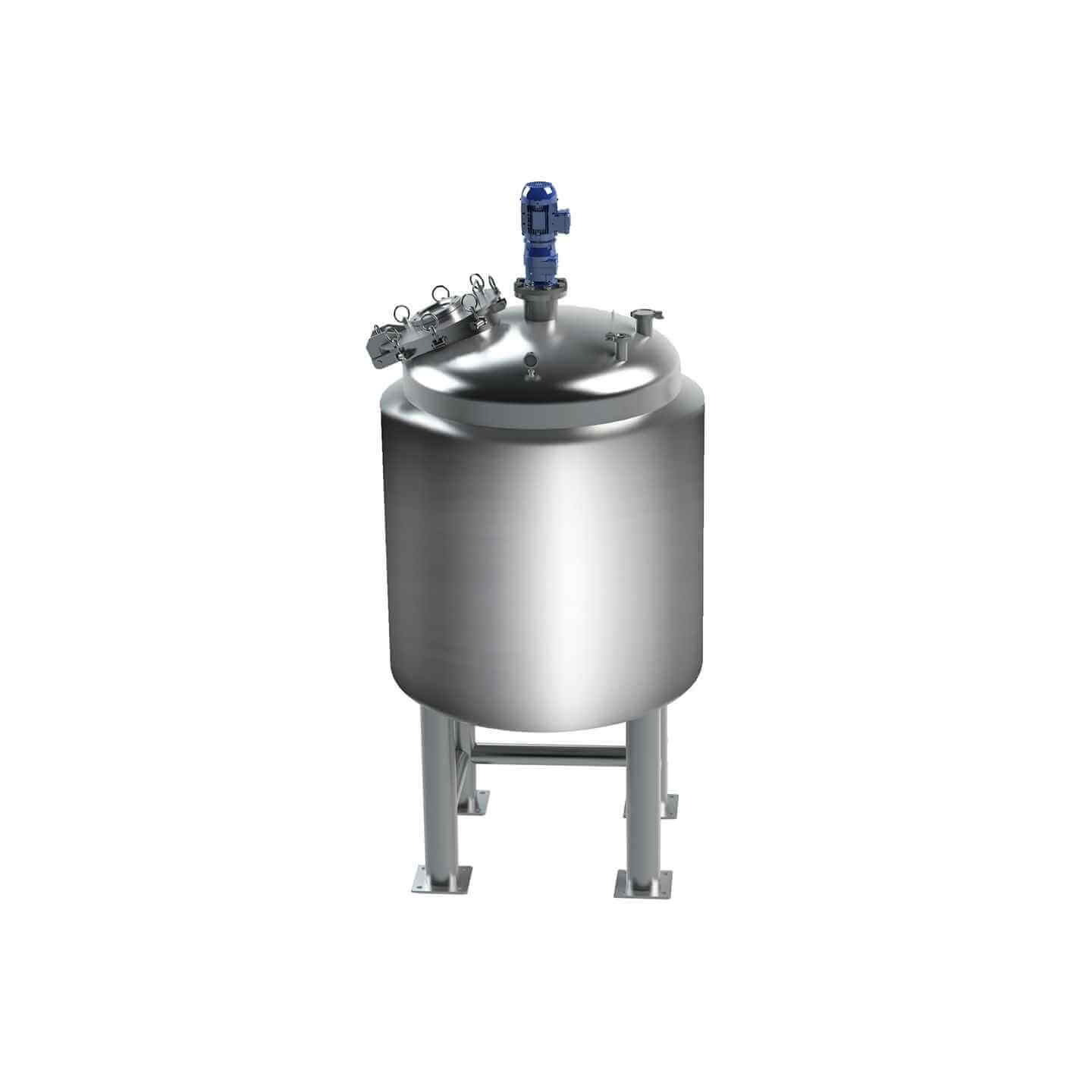
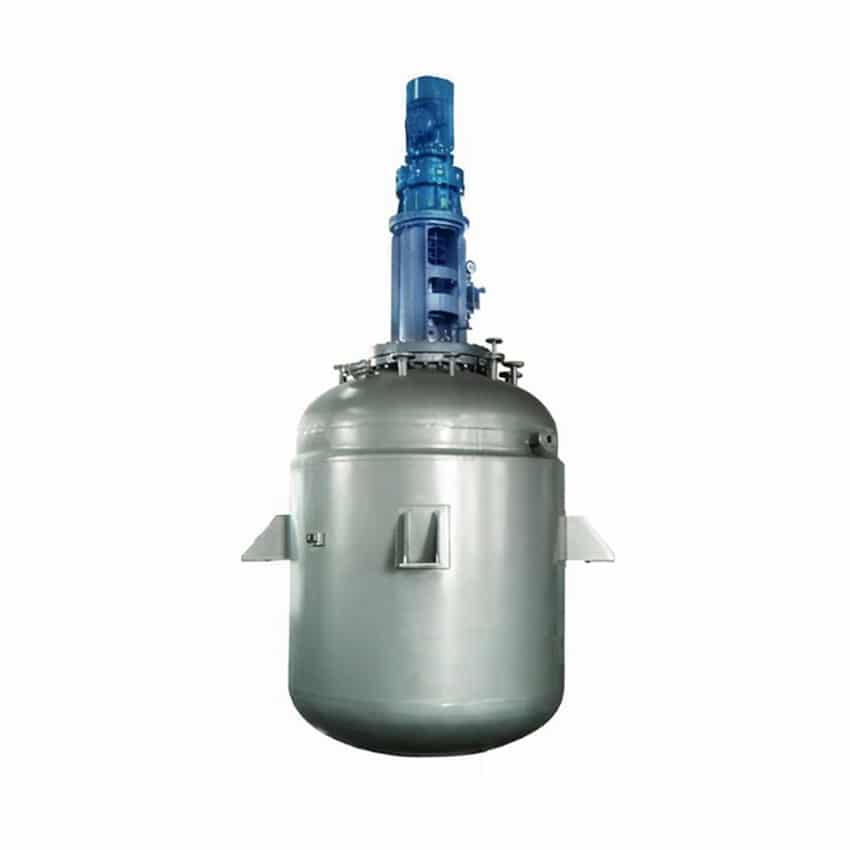
Jacketed Reactor
Jacketed reactor: used in the chemical industry, pharmaceutical industry and food industry, and other fields
Material
glass, stainless steel (316, 304), carbon steel, others
Capacity (L)
10-10000+
Mixing system
anchor, paddle, frame and others
Heating system
electric heating, oil heating and others
Jacketed reactors can be divided into steam heating reactors and heat transfer oil heating reactors according to different heating media, both of which are widely used in medicine, the chemical industry, plastics, rubber, building materials, food, and other industries. Corrosion, no environmental pollution, no need for automatic boiler heating, ease to use, and so on.
Request a quoteThe jacketed reactor is mainly composed of a kettle body, a kettle cover, a jacket, a stirrer, a transmission device, a shaft seal device, a bracket, etc. Among them, the commonly used jacket type for jacketed reactors is generally called an integral jacket.

Characteristics of jacketed reactor
1.Each component of the jacketed reactor is equipped with a jacket. Generally speaking, this is suitable for occasions where the heating area is small;
2.The jacketed reactor body and lower head are equipped with jackets, so the heating area is large, and it is a very commonly used jacket structure;
3.Considering that when the jacketed reactor is subjected to external pressure, firstly, in order to reduce the calculated length of the cylinder, and secondly, to better achieve the heat transfer effect of segmented control, the segmented jacket type can generally be used;
When customizing a jacketed reactor, the most appropriate jacket structure can be selected based on actual working conditions, including economic budget and other aspects. According to factors such as the diameter of the jacket or the standard of the selected head form, the connection method between the overall jacket and the cylinder can be divided into detachable jackets and non-detachable jackets, but there are usually a variety of non-detachable jackets. Removable jacket made from the chemical reactor.
The jacket of the jacketed reactor is also equipped with a nozzle to facilitate the entry and exit of the heat transfer medium and gas. This is the same as ordinary containers, which are more convenient, and the discharge port on the entire jacket does not require special treatment. For the jacketed inlet pipe, measures should be taken to weld an additional baffle on the jacket wall. When installing the nozzle on the jacket, it should be noted that the opening area of the water inlet pipe or steam baffle should not be smaller than the cross-sectional area of the nozzle channel.
The dangers of not cleaning the jacketed reactor
1.Once the mechanical shaft seal of the jacketed reactor is contaminated by dirt, a series of dangerous phenomena such as liquid leakage and gas injection will occur.
2.The heat exchange function of the uncleaned jacketed reactor is low and the reaction time is increased. Dirt attached to the inner wall of the kettle will greatly reduce the heat exchange performance, prolong the reaction time, and reduce product quality.
3.Dirt on the thermometer will delay temperature measurement and affect the reaction control system.
4.Dirt attached to the stainless steel reactor bearings and the back of the jacketed reactor will damage the mechanical shaft seal.
5.The internal and external surfaces of the jacketed reactor, especially the gaps that harbor dirt and evil. The concentration of the liquid will create a certain battery effect, thereby corroding the surface where dirt adheres. This will further aggravate the corrosion of the jacketed reactor and ultimately affect the service life of the equipment itself.