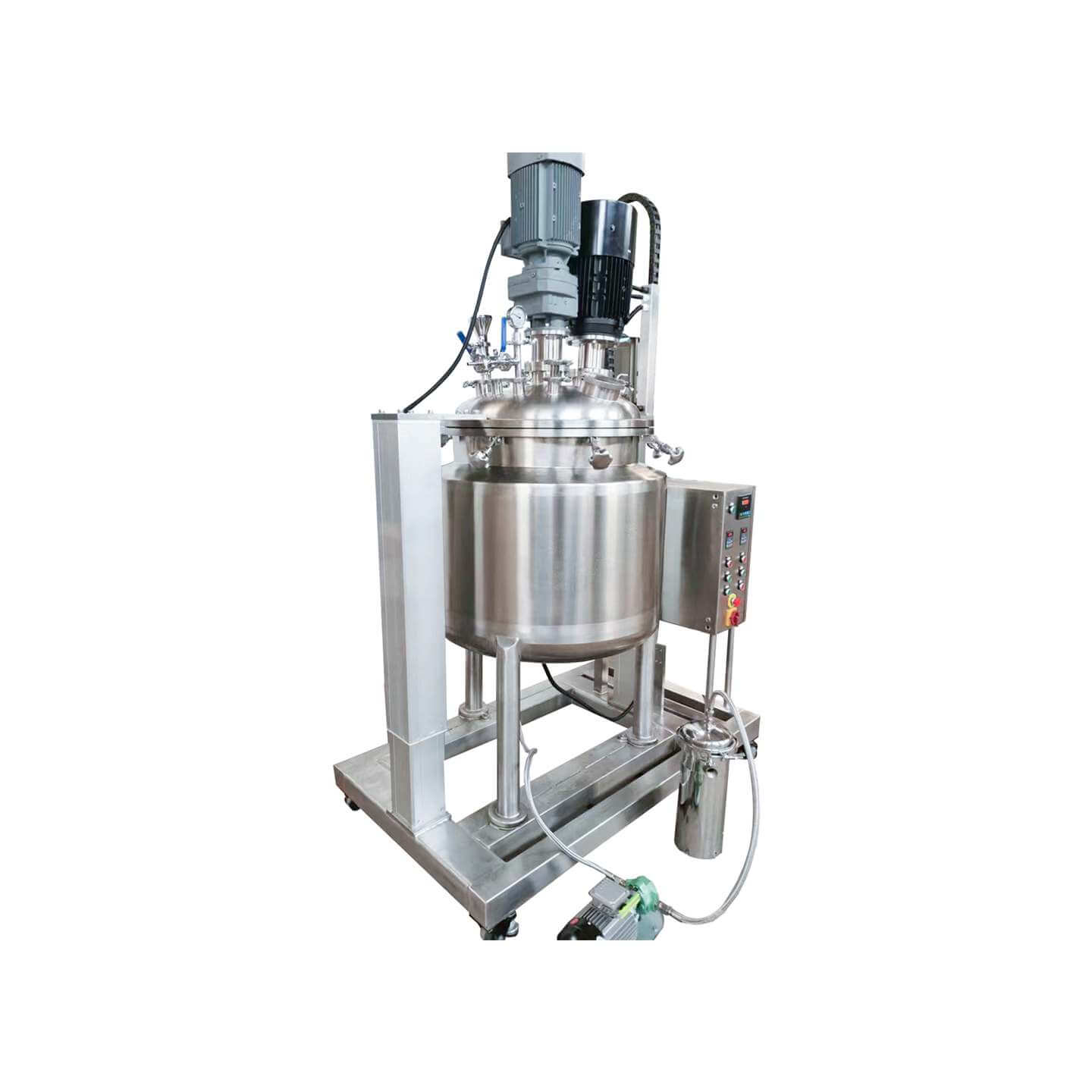
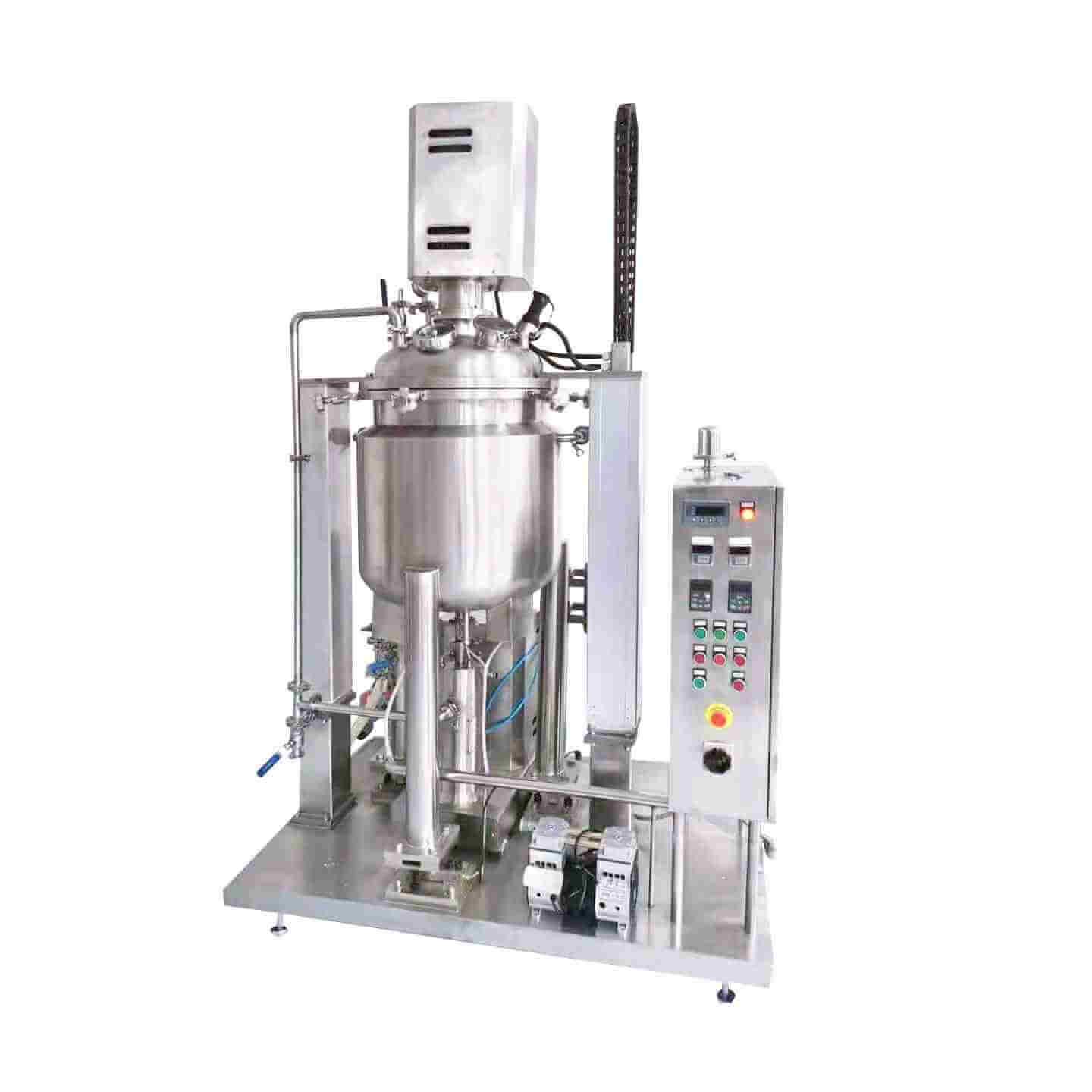
Laboratory Reactor
Laboratory reactor: used in the chemical industry, pesticide, paint, and other fields
Material
glass, stainless steel (316, 304), carbon steel, others
Capacity (L)
10-10000+
Mixing system
anchor, paddle, frame and others
Heating system
electric heating, oil heating and others
The laboratory reactor is small in size, beautiful in appearance, light, and fast in installation. It is composed of a pot body, pot cover, stirrer, jacket, support and transmission device, shaft sealing device, etc. The type of stirring device, rotation speed, sealing structure, heating method, etc. are produced.
Request a quoteDue to differences in production processes and operating conditions, laboratory reactors require holes in the lid and cylinder. Laboratory reactors have different requirements for the mixing type (paddle type, anchor type, frame type, screw type, etc.), support type (suspended or supported type, valve seat type, etc.), and sealing device.

Precautions for using laboratory reactors
1.It should be operated and used strictly according to the working pressure and working temperature calibrated on the product nameplate to avoid danger.
2.Strictly abide by the regulations on cooling, oil filling, etc. in the instruction manual of the laboratory reactor, and do a good job in the maintenance and upkeep of the equipment.
3.When using all valves of the laboratory reactor, the valve stem (needle) should be rotated slowly and the valve cover should be pressed tightly to achieve a sealing effect. Do not use excessive force when closing to avoid damaging the sealing surface.
4.Electrical control instruments should be operated by dedicated personnel, and overload protection facilities should be installed in accordance with regulations.
Common fault phenomena and causes of laboratory reactors
1.Fault phenomenon: Leakage occurs on the sealing surface. Cause of failure: loose thread; damaged sealing surface. Troubleshooting method: Re-tighten the screws; re-grind and polish the sealing surface.
2.Fault phenomenon: There is leakage at the valve. Cause of failure: The valve stem (needle) and valve port sealing surface are damaged. Troubleshooting method: Repair or replace the valve stem (needle) and valve port.
3.Fault phenomenon: The outer magnet rotates, the inner magnet does not rotate, and the motor current decreases. Cause of failure: The temperature inside the kettle rose too high, the cooling cycle was not smooth, and the internal magnet steel demagnetized due to high temperature. During the hydrogenation reaction, cracks appeared in the inner magnet steel sleeve and the inner magnet steel expanded. Troubleshooting method: Notify the supplier and replace the inner magnet.
4.Fault phenomenon: There is friction noise in the magnetic coupling transmission. Cause of failure: The shaft sleeve and bearing are worn, the gap is too large, and the inner magnet is rotating. Troubleshooting method: Contact the supplier to replace the bearings and sleeves.
Installation and use of laboratory reactor
1.The laboratory reactor should be installed on a solid, flat workbench. The height of the workbench is determined according to its purpose. A certain amount of space (≥360cm) should be left around the equipment and workbench to facilitate installation and subsequent maintenance.
2.When installing the laboratory reactor, the transmission shaft is required to be vertical to the ground, and the non-verticality (inclination) must not be greater than 1/1000 of the total height of the equipment.
3.The spare parts and safety valves on each process connection of the laboratory reactor must be equipped according to the requirements of the laboratory reactor.
4.After the laboratory reactor is installed, check whether the connecting parts and transmission parts are firm and reliable. The air tightness test of each connecting pipe, nozzle, seal, and the whole machine should be free of bubbles, bubbling, dripping, and leakage.
5.Before starting up, inject 46# mechanical oil into the reducer. Open the motor protective cover, turn the fan blades by hand, check whether there is any jamming, whether the stirring paddle scrapes the wall, and clean the dirt in the laboratory reactor before starting the machine. After the empty car runs for 30 minutes without abnormal noise or vibration, it can be officially put into production. In addition, the reducer oil should be replaced regularly according to production conditions.