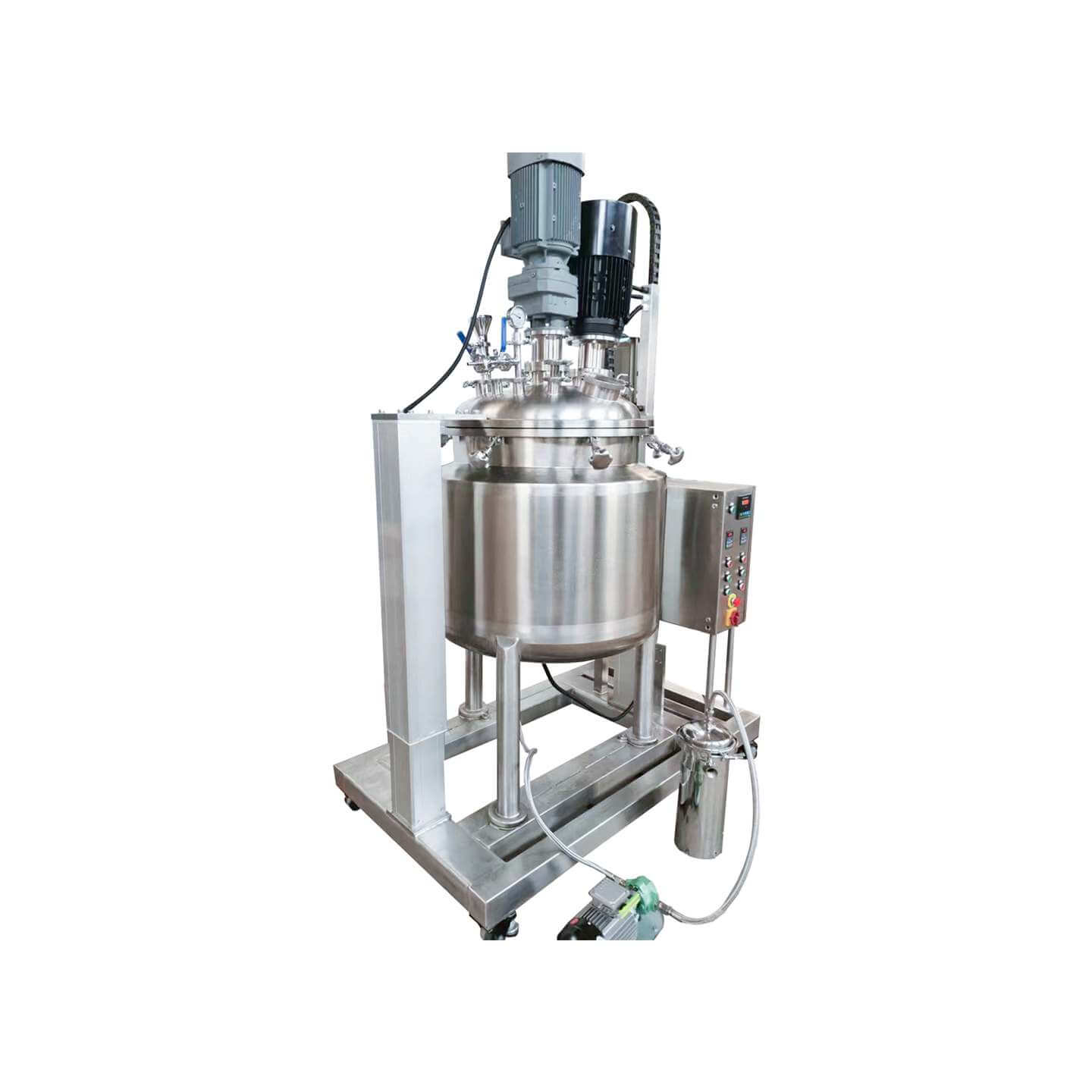
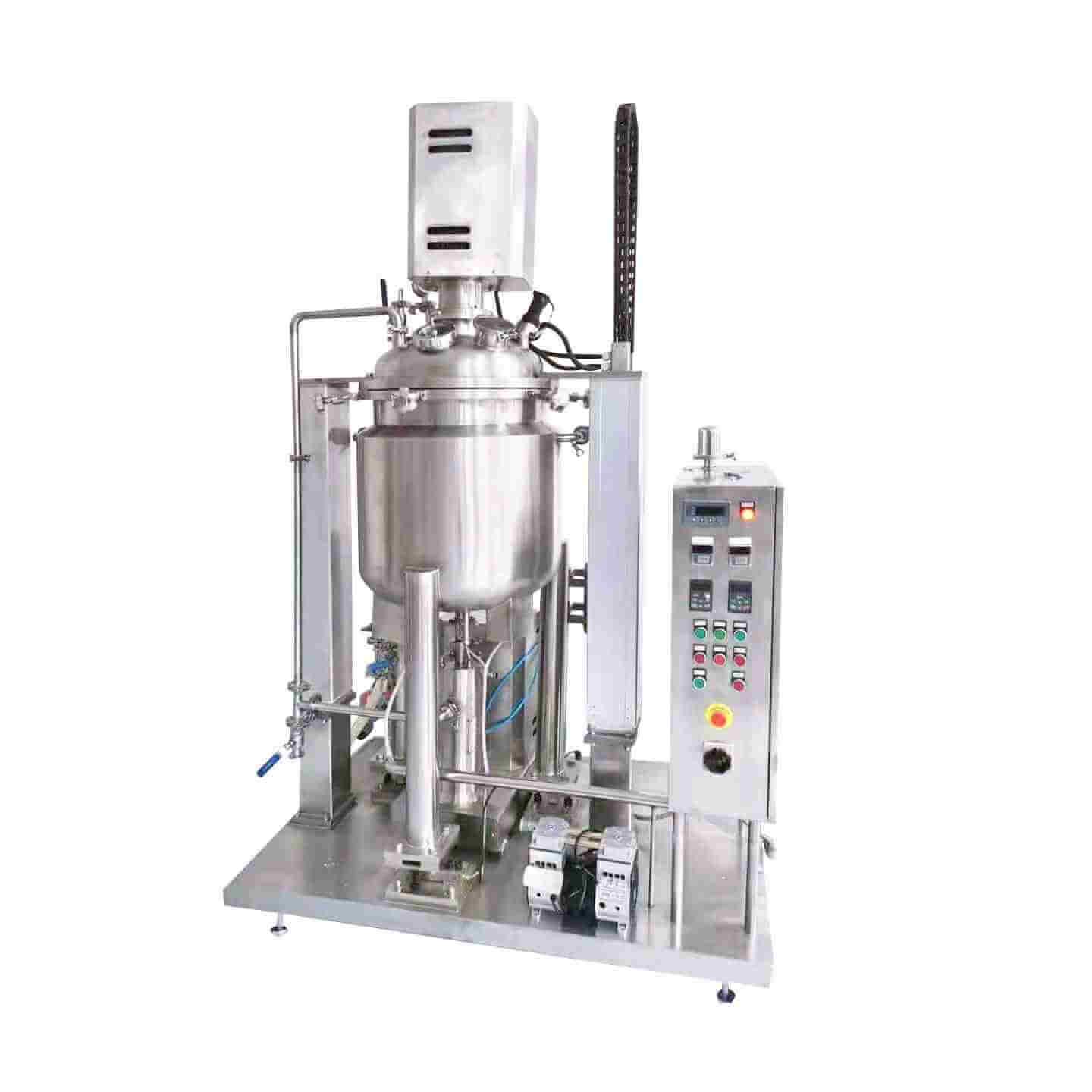
Laboratory Reactor
Laboratory reactor: used in the chemical industry, pesticide, paint, and other fields
Material
glass, stainless steel (316, 304), carbon steel, others
Capacity (L)
10-10000+
Mixing system
anchor, paddle, frame and others
Heating system
electric heating, oil heating and others
The laboratory reactor is small in size, beautiful in appearance, light, and fast in installation. It is composed of a pot body, pot cover, stirrer, jacket, support and transmission device, shaft sealing device, etc. The type of stirring device, rotation speed, sealing structure, heating method, etc. are produced.
Request a quoteLaboratory reactors are typical equipment used in chemical, pharmaceutical, and food industry plants. The laboratory reactor produced by RUNGYU is mainly a hydrolysis reaction kettle in the production process of para-nitro and is used for the hydrolysis reaction process of para-nitro. Its stirring can disperse two or more different substances with each other to achieve uniform mixing; it can also accelerate the process of heat transfer and transmission.
The mixing method of the laboratory reactor is very simple. Mainly used in chemical laboratories when preparing saline solutions, use glass rods to stir the liquid in the beaker to accelerate dissolution. Widely used as part of the process, mixing operations are divided into mechanical mixing and airflow mixing.

In industrial production, laboratory reactor stirring operations began in the chemical industry, centered on food, fiber, papermaking, petroleum, water treatment, etc. Airflow stirring uses gas to bubble through the liquid layer to stir the liquid. Most mixing operations in industrial production are mechanical mixing. However, bubbles have a very weak effect on liquid stirring and are not suitable for high-viscosity liquids. The mixing equipment mainly consists of three parts: mixing device, shaft seal, and mixing tank.
Laboratory reactor stirring equipment is widely used in industrial production, especially in the chemical industry. Many chemical productions use stirring operations to a greater or lesser extent. In many cases, stirred devices are used as laboratory reactors. For example, in the production of the three major synthetic materials, mixing equipment accounts for about 90% of laboratory reactors. Mixing equipment is also widely used in other industries such as dyes, medicines, pesticides, coatings, etc. Various chemical changes in chemical processes are predicated on the complete mixing of reactants.
Various chemical changes in chemical processes are predicated on the complete mixing of reactants. The reason why the application range of laboratory reactor stirring equipment is so wide is that the operating conditions (such as concentration, temperature, residence time, etc.) of laboratory reactor stirring equipment can be controlled in a wide range. For physical change processes such as heating, cooling, liquid extraction, and gas absorption, some effects can only be achieved through stirring operations. Can adapt to diversified production. Laboratory reactors are mainly used in hydrolysis, neutralization and crystallization, distillation, evaporation, storage, and other production processes in medicine, bioengineering, fine chemicals, chemical synthesis, food, and other industries. They are a commonly used reaction vessel with a simple structure. The operation is simple and the structure is simple.

Structure and materials of laboratory reactor
Laboratory reactor equipment is mainly composed of three parts: tank, shell and stirring system. The parts in contact with materials are made of high-quality stainless steel such as 304 or 316L, complying with GMP standards. Its heating method can be steam, electric heating, thermal oil, etc. to meet the process requirements of different working environments such as acid resistance, high temperature resistance, wear resistance, and corrosion resistance. The inner surface of the laboratory reactor is mirror polished, while the outer surface can be sandblasted, frosted or cold-rolled to ensure that there are no sanitary dead corners. The fully enclosed design of the laboratory reactor ensures that the materials are always in a sterile state.