
-24-1.jpg)
Stainless Steel Reactor
Stainless Steel Reactor: used in dairy products, sugar, beverages, and other fields
Material
stainless steel (316, 304)
Capacity (L)
10-10000+
Mixing system
anchor, paddle, frame and others
Heating system
electric heating, oil heating and others
A stainless steel reactor is a stainless steel container equipment. The stainless steel reactor consists of a kettle body, a kettle lid, a stirrer, a jacket, a bracket, a transmission device, a shaft seal device, etc. Materials and openings can be made according to user needs and process requirements. Stainless steel reactors are mainly used for stirring, homogenizing, and mixing storage of dairy products, sugar, beverages, food, and various pharmaceuticals.
Request a quoteThe fully enclosed design of the high pressure stainless steel reactor can keep the materials in a sterile state, making it fast heating, high-temperature resistance, corrosion resistance, hygienic, no environmental pollution, no need for automatic boiler heating, easy to use, low price, etc. Therefore, the stainless steel material of the high pressure stainless steel reactor needs to be deeply processed to maintain its high quality and good experience in function and use. The surface treatment technology of high pressure stainless steel reactor is divided into: pretreatment, oxide scale removal and pickling, polishing, electroplating, high-temperature anti-oxidation coating, passivation, coloring, chemical coloring, chemical and electrochemical corrosion processing, etc.
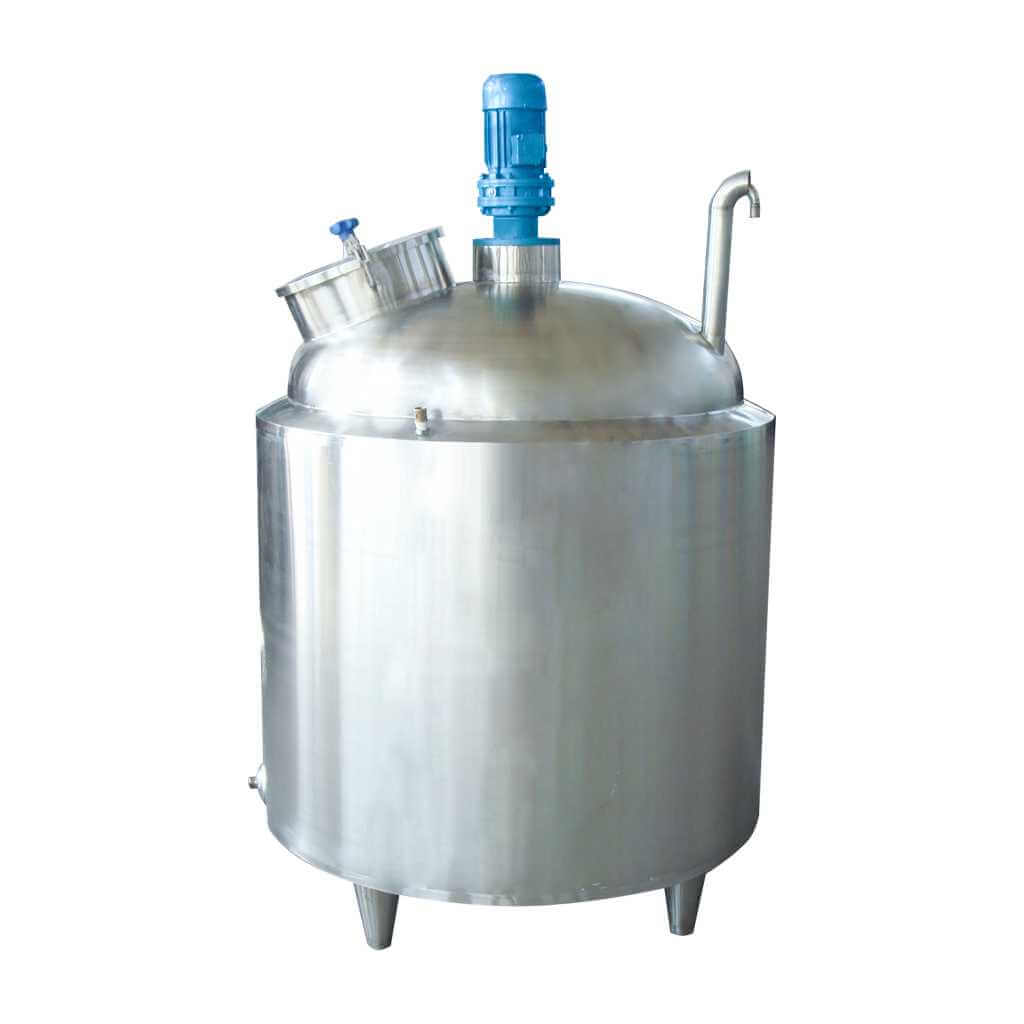
Surface treatment method of high pressure stainless steel reactor
Due to the special metallographic structure and surface passivation film of the high pressure stainless steel reactor, it is generally difficult for it to chemically react with the medium without being corroded, but it does not mean that it cannot be corroded under any conditions. Therefore, it is very important to understand the surface treatment methods of high pressure stainless steel reactors. The main methods are as follows:
1. Surface coloring treatment: Coloring of high pressure stainless steel reactors not only gives stainless steel products various colors and increases the variety of product styles, but also improves the wear resistance and corrosion resistance of the products;
2. Surface mirror brightening treatment: Depending on the complexity of the high pressure stainless steel reactor and user requirements, mechanical polishing, chemical polishing, electrochemical polishing, and other methods can be used to achieve mirror gloss;
3. Surface spraying of micro-glass beads: It can remove the black oxide scale on the surface of high pressure stainless steel reactor, which is also very applicable now;
4. Surface chemical treatment: Use a pollution-free pickling passivation paste and a normal temperature non-toxic cleaning solution with inorganic additives for soaking and cleaning. In this way, the purpose of whitening the original color of stainless steel can be achieved. After treatment, it basically looks almost matte. This method is more suitable for large and complex products;
5. Surface whitening treatment: During the processing of stainless steel, a black oxide scale is produced after rolling, edging, welding, or artificial surface heating. This hard gray-black oxide scale is mainly composed of NiCr2O4 and NiFeO4. In the past, hydrofluoric acid and nitric acid were often used for strong corrosion removal. However, this method is costly, pollutes the environment, is harmful to the human body, and is highly corrosive, so it will be gradually phased out.

Because the microscopic convex parts and concave parts on the surface of the high pressure stainless steel reactor have different conditions for film formation and passivation, and due to the dissolution of the anode, the concentration of metal salts in the anode area continues to increase, forming a high-resistance thick mucosa on the surface. The different thicknesses of the film at the concave and convex places result in a high current density on the anode surface and a fast discharge and dissolution rate at the top. It can achieve the purpose of flattening the protruding microscopic parts in a short period of time and can achieve a very high smoothness Ra≤0.2-0.4μm. And under this effect, the corrosion resistance of the passivation layer on the metal surface of the high pressure stainless steel reactor is increased.
After the internal and external surfaces of the high pressure stainless steel reactor are electrolytically polished and mechanically polished, they will have a good passivation layer and enhanced corrosion resistance. The higher the smoothness of the internal and external surfaces of the high pressure stainless steel reactor and the less adhesion of the medium, the better it will be for corrosion resistance. The higher the smoothness of the inner surface of the reaction transfer tube, the less the liquid medium will be retained, and the more conducive it is to flushing, especially in the pharmaceutical industry. The surface treatment of high pressure stainless steel reactors should choose different methods according to the product structure, material quality, and surface requirements.